Operations Excellence

Most manufacturers have operations teams skilled in the core methodologies to improve efficiency and quality—Lean Six Sigma, Kaizen, TPS and Kanban. But it is rare to see Agile teams working their magic on the shop floor or the supply chain. In fact, only 2% of teams that use Scrum, the most popular form of Agile, are in operations functions, according to Scrum Alliance.
That’s a lost opportunity. Large projects under Agile management are six times more likely to succeed than non-Agile projects, research shows. Companies that have used Agile teams say they are more productive and faster to market. They reduce project risk, manage changing priorities better and increase team motivation (see Figure 1).
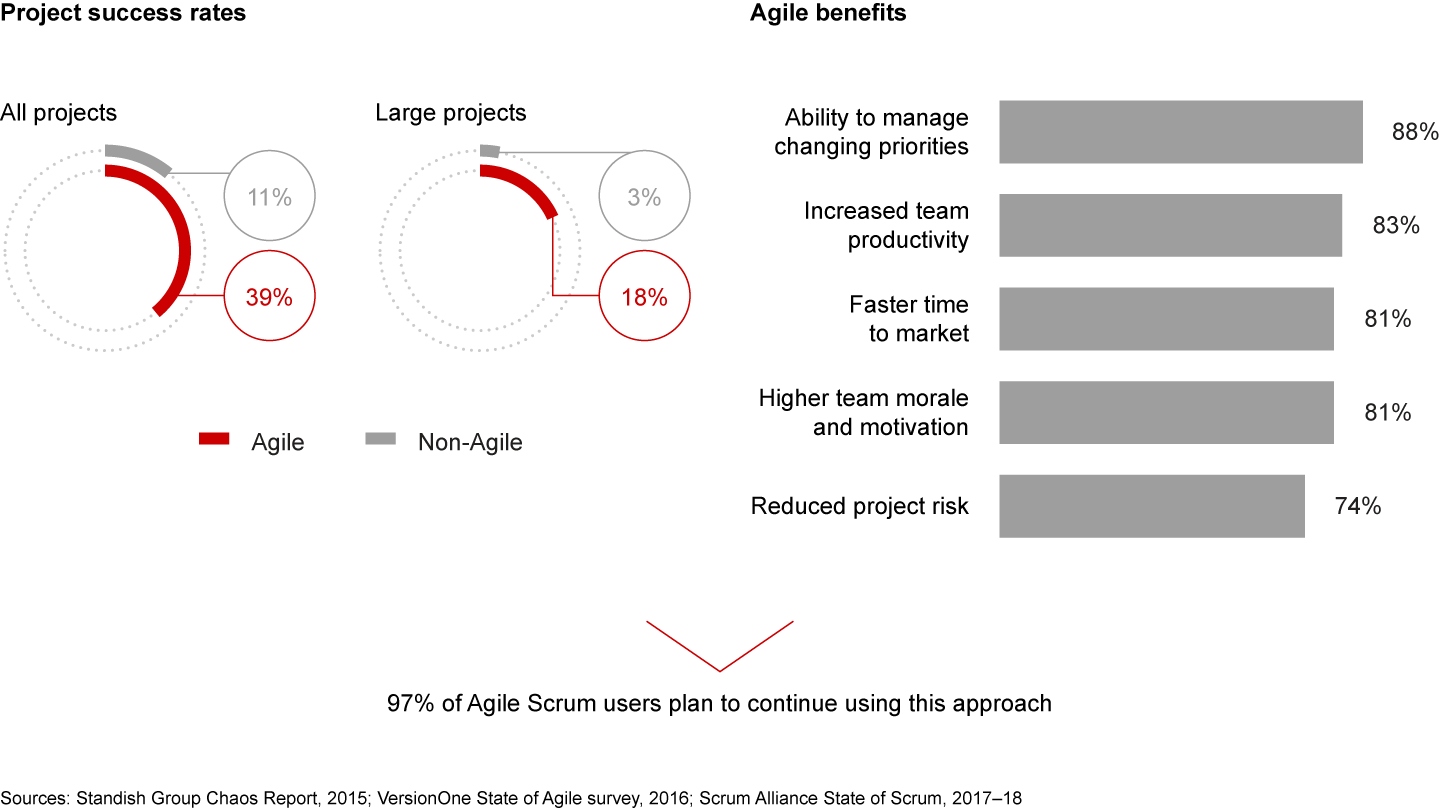
True, Agile is best known for its success in speeding new product development in software and IT. But Agile methodology has its roots in operations. Manufacturing organizations including Toyota, Bell Labs and Lockheed Martin’s Skunk Works were the first to deploy Agile-like concepts such as cross-functional teams that break down work into small increments and quick sprints of one to four weeks to develop solutions.
The challenge with transforming operations, of course, is the complexity it entails. Chief operating officers, supply chain heads and plant managers have their hands full juggling the firm’s strategic and productivity goals. They may be reluctant to launch big change efforts if they require expertise that is spread across geographies and functions. Another concern: the resources and time required to implement a successful change program.
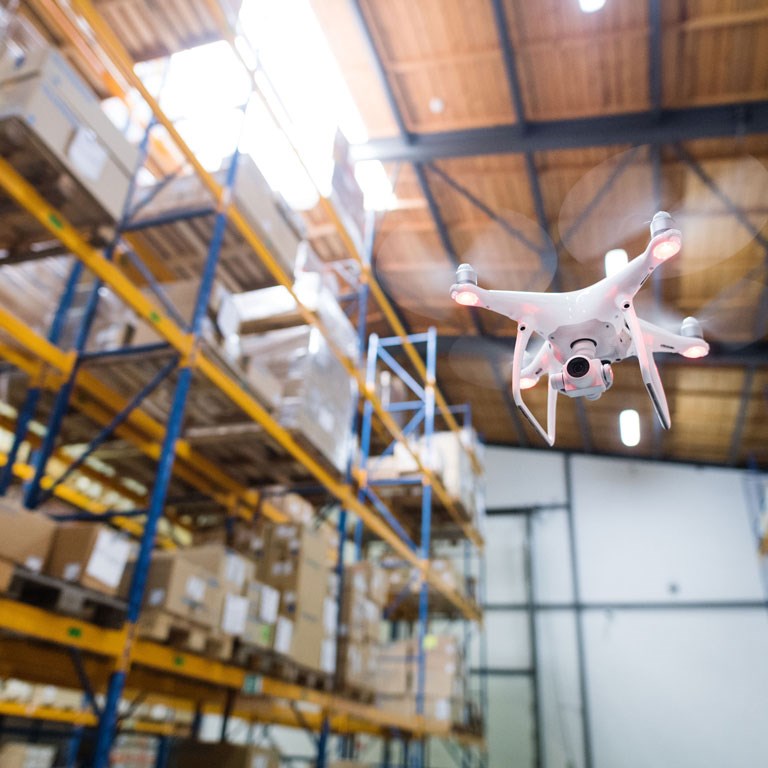
Operations Excellence
Companies with best-in-class operations have a strong competitive edge. Bain's insights on operational excellence help leadership teams transform supply chains, procurement strategy, and manufacturing capabilities into strategic weapons.
Take the case of a global consumer-packaged-goods company that had been discussing for years the need to reduce product complexity, streamline packaging and improve transportation efficiency. The company routinely sent more than a dozen 5-kilo cartons to the same customer on the same day, often with different trucks. Shifting to one large container, fuller trucks and fewer deliveries could have reaped big savings and increased customers’ efficiency. But the leadership team anguished about the complexity involved in rethinking its processes. Changing transport packaging at multiple plants simultaneously was daunting, especially since plant resources were constrained.
When the idea came around again in 2017, increasing complexity and costs persuaded the senior executives to create a cross-functional Agile team including engineering, operations, and finance experts to quickly develop a solution. It focused first on creating a tool to gauge the benefit of right-sizing transport packaging for each product. The next step was designing alternative transport packaging.
After designing one product in one geography, the team made a convincing case to management to deploy the new approach at all its plants. The Agile team initiated packaging redesign at more than six plants in nine months, saving more than $10 million in the first year. The packaging initiative also resulted in significant savings for the company’s customers.

Doing Agile Right
Our latest book is a must-have guide to transform your organization through the power of agile...the right way.
In addition to unlocking significant value, the Agile team completed the project five times faster than the company’s traditional global project planning and deployment. The success of the packaging-redesign initiative convinced senior executives to deploy Agile teams in other areas of operations, including redesigning the sales- and operations-planning process.
Agile teams develop and implement solutions faster because they are self-managing and have the decision-making authority to achieve bold goals. To make sure Agile teams are effective, senior executives need to give the team ambitious targets and then empower them to make decisions, fail fast and incorporate what they learned into the next solution. Leadership teams also need to include them when setting priorities. Ultimately, Agile teams free senior operations leaders from micromanaging change efforts so they can spend more time on strategic issues.
Traditional operational excellence methodologies such as Lean Six Sigma or Kaizen are great for achieving ongoing and incremental productivity gains. But when leadership teams want rapid innovation that creates a step change in operations performance, Agile teams are more effective.
One example is the shift to digital operations that many companies will make over the next three to five years. As senior executives rethink operations from top to bottom, Agile teams can help them test digital solutions and learn quickly, reduce risk and succeed more often.
Richard Spady and Josh Hinkel are partners in Bain & Company’s Performance Improvement practice. Richard is based in the firm’s Atlanta office, and Josh is located in the Dallas office.