Brief
Executive Summary
- Compared with other industries, chemical companies have underdeveloped pricing capabilities. They are less confident in their pricing decisions and less likely to raise prices regularly.
- Chemical companies can improve pricing capabilities by understanding the customer’s business better and the role of their products in it, so they can price according to value rather than on a cost-plus basis. Most will also need to become more nimble, so they can respond to market fluctuations and opportunities with dynamic pricing.
- Many chemical companies will also need to revise their sales incentives, to encourage profitable deals rather than rewarding mere volume sales.
Compared with other industries, chemical companies are among the least confident in their pricing decisions and the least likely to raise prices regularly (see Figure 1). Until recently, these shortcomings haven't hurt their financials; many have maintained healthy margins even with limited volume growth, thanks to low prices for many raw materials, especially in western markets.
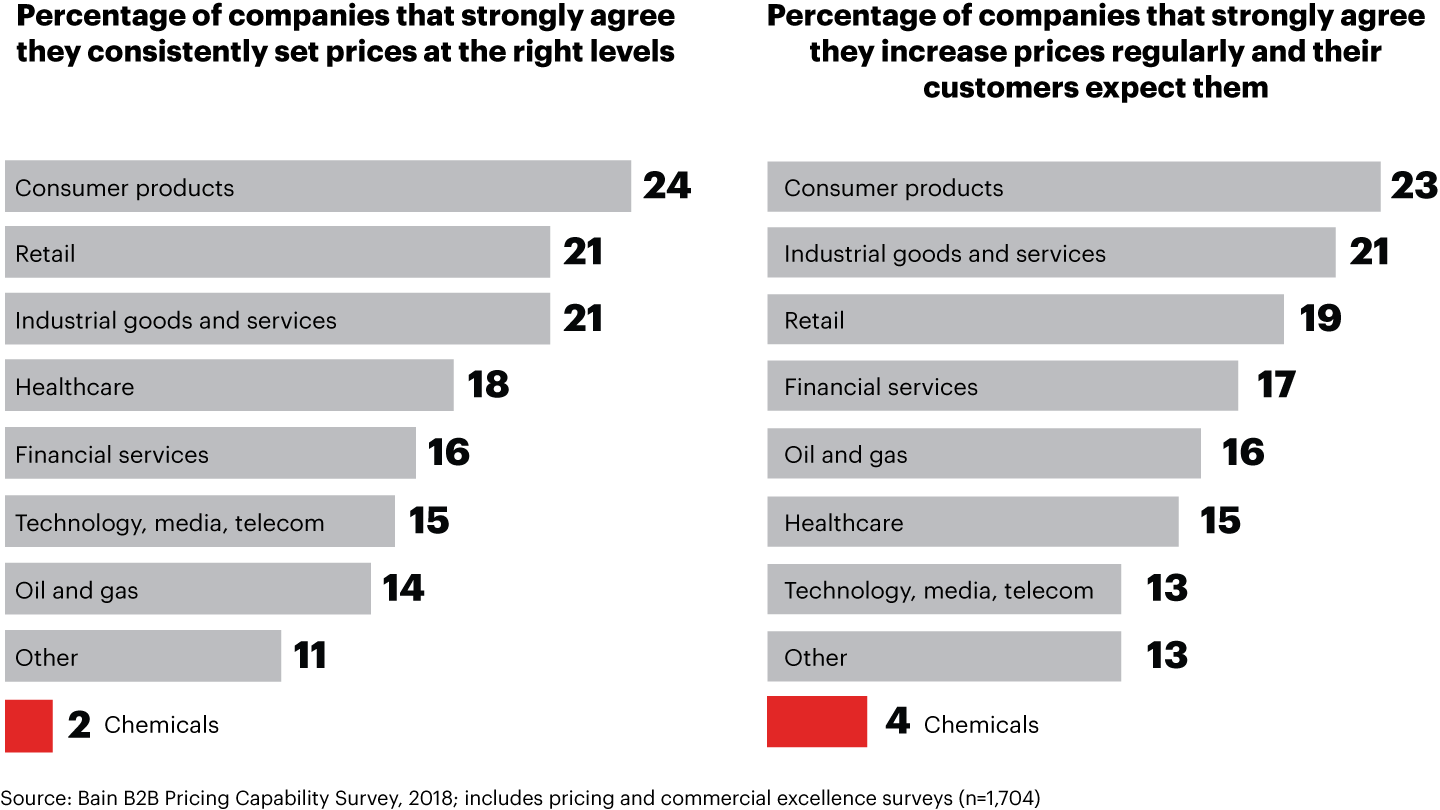

Looking ahead, however, chemical companies will need to learn to exercise their pricing muscles again simply to maintain margins, as several pressures converge. First, the costs of raw materials, crude oil in particular, have risen steadily. Freight costs are also rising as requirements for electronic logs in the US take capacity off of the road. In addition, uncertainty over tariff increases on petrochemicals, specialty chemicals and plastics also raises the pressure on chemical producers to improve their pricing capabilities.
In an environment like this, protecting margins is necessary, but not sufficient. Instead, companies should be reaching higher, aiming for full potential pricing capabilities that actually expand margins. That won't be easy for chemical producers. A lack of management focus on pricing, combined with misaligned incentives, have left chemical executives far behind their peers in other industries in terms of seizing opportunities to increase profitability through pricing. But the prize is worth pursuing: Our research finds that improving pricing capabilities typically adds 200 to 400 basis points to the bottom line—a significant impact in an industry where margins average 10% to 12%.
Bain researched pricing practices and behaviors by surveying more than 1,700 executives across sectors, including the chemical industry. Our findings should help executives identify and recognize weaknesses in their own organizations, and begin to take steps to improve them.
Dave Schottland, a partner with Bain's Chemicals practice, describes the three methods best-in-class companies use to make pricing decisions that bring results.
Know your worth
Historically, the chemical industry has relied too heavily on cost-plus pricing or models that reflect only a partial understanding of the value of their products to customers' businesses. Many pricing decisions also fail to consider competitors' actions. Some commodity chemical producers believe they are destined to be price takers, selling into competitive markets with razor-thin margins. They overlook the value of their commercial relationships, their reliability, the quality of their products, or other capabilities that would allow them to set prices that maximize margins. This critical information often lives somewhere in the organization, but unfortunately not always where pricing decision makers can find it. One chemical company learned from its own technology service team that its additive was critical to removing heavy metals and thus vastly increased the life of a customer's turbines. Another learned from its customer service team that its product was specified in a customer's formulation and so had no simple substitutes. Still another learned from its supply chain team that its unique packaging created tremendous efficiencies for a customer's unloading time. All of these are sources of value that could be captured better by these chemical companies.
Yet capturing this information and simply identifying pricing opportunities is not enough. Most chemical companies are slow to take action on pricing even though evidence suggests they could move more rapidly. This resistance stems from concerns about losing volumes, misaligned incentives and the legacy of an "order taker" mindset in the front lines. By adopting a test-and-learn approach, these companies can change prices, collect feedback and refine their pricing approach, effectively retraining customers to become comfortable with dynamic pricing. Market leaders are increasingly gaining the confidence to set market expectations about price, and they schedule a cadence of price increases once or twice a year in ways that the value chain can absorb. Fears about losing business to competitors in low-cost regions become less potent as customers come to value their commercial relationships with suppliers and recognize the value they add through quality and reliability of supply.
A formula for pricing success
Firms that harness the formula for best-in-class pricing in chemicals greatly outperform on pricing outcomes. They consistently raise prices over time and across their customer base, expanding margins above and beyond their costs. And they are increasingly nimble in reacting to opportunities and challenges in market fluctuations, executing price changes quickly to preserve and improve yields (see Figure 2). Top performers show common patterns.
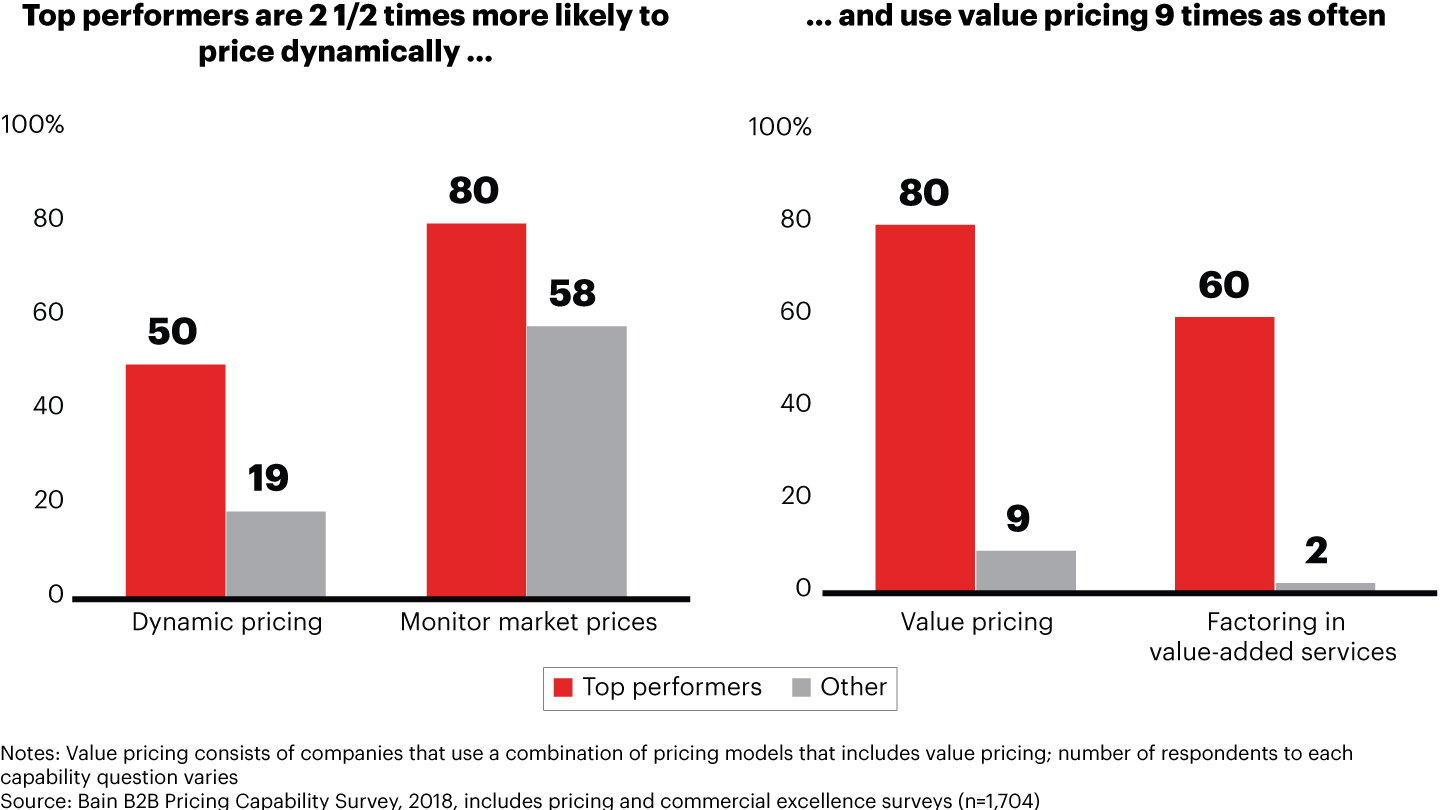

- Price to reflect value. Pricing leaders broaden the conversation with their customers beyond price, to get a better understanding of the value their products add to their customers' business. By learning what customers value and what they're willing to pay for, leaders can set the right target price for each product for each customer. They also learn what trade-offs they can make: some customers would pay more for better service, while others want a low-touch, low-price option. Both can deliver attractive economics, if managed carefully.
- Dynamic pricing. Leaders are more than twice as likely to use dynamic pricing, reacting quickly to changes in the market and taking full advantage of upswings and downturns. They forecast changes in input costs before they occur, monitor supply and demand dynamics, and have a sense for how customer demand is evolving. In addition, best-in-class companies know exactly which customers and products make money, which don't, and why. This helps them decide where to be more or less aggressive with pricing, in order to expand margins opportunistically. Importantly, the critical actions that turn this analysis into revenue are regular, cross-functional forums where teams review these insights and make nimble pricing decisions. One packaging distributor found that passing along cost increases quickly and giving back cost decreases slowly was worth an additional 50 to 100 basis points of EBITDA, compared with the closest competitor.
- Effective incentives and rewards for good pricing behavior. Leaders offer their sales teams incentives that reinforce the importance of profitability, rather than merely encouraging sales volume or revenue growth. Of course, incentives shouldn't focus solely on margin; orders from even low-profitability customers are an important part of the mix that keeps assets running at high utilization rates. To achieve this balance, companies can deploy pricing tools that guide sales teams and provide a target range that permits some flexibility. Management can flex the incentive scheme's emphasis on price or volume, depending on market conditions and asset utilization.
- Senior management focus. Of course, as with every important initiative, no pricing initiative can reach its full potential without strong and visible commitment from senior executives. Our survey found pricing leaders are 42% more likely to make pricing a top management priority. One chemicals materials company makes pricing a key agenda item during the CEO's monthly implementation meeting. Pricing actions have their own pipeline, are monitored in a stage-gate process, and are as much a part of the executive conversation as major capital projects, cost initiatives, development projects and the sales pipeline. This visibility and rigor ensures that pricing changes are highly visible, and the company doesn't count the value until it shows up on income statements.
Our study found large gaps in senior management's commitment to pricing as a critical topic. This lack of visibility may be a byproduct of the industry's traditional focus on operational efficiency, safety and cost removal—areas of excellence that reflect the engineering strengths of management teams in this industry. Having achieved operational excellence, executive teams can now expand their focus to commercial excellence, including pricing.
There's never a bad time to improve pricing capabilities, but there's no better time than now. Companies that don't act may find themselves struggling to maintain margins as the costs of raw materials and freight rise. But those companies that follow the formula for pricing success—pricing to value, adopting dynamic pricing and realigning incentives—can outperform the market and maintain a healthy bottom line.
David Burns is a partner with Bain & Company in Chicago, and David Schottland is a principal in New York. Both work with Bain's Global Chemicals practice.