Operations Excellence
One of the core tenets of lean production is fostering continuous improvement from the bottom up. Thirty years since the lean revolution began, most companies have taken that principle to heart, empowering employees to help manage, smooth and improve processes by eliminating waste. Done well, lean programs can create a leap in performance, but our experience shows many fail to deliver the expected results.
Here’s the paradox: When lean initiatives go wrong, it’s often because the bottom has too much control, and little or no input from above. Without guidance, enthusiastic shop floor workers may embark on a huge number of improvements at one go. Some management teams make that same error by forcing too much change from the top down.
Imagine what it must be like on the production line of a company that has launched dozens of lean initiatives. Suddenly, workers must change the way they do almost everything. However, supervisors, line managers and workers all have limited capacity to absorb change to existing routines. Introducing too many initiatives at once overwhelms organizations with complexity—and obscures the few changes that matter most. The result is confusion and disorder.
Take the case of a global industrial company that launched a lean program to improve its overall equipment effectiveness (OEE) and achieve world-class manufacturing performance. The company set out to implement more than 30 lean tools simultaneously. But the complexity involved in carrying out all those new initiatives overburdened shift supervisors, line managers and workers. The program quickly ground to a halt.
In our experience, lean programs that deliver powerful results concentrate on the two or three changes that create the most business value. Line managers select the best ideas—those that will have a significant impact on the bottom line and simplify work processes on the shop floor. That critical step helps companies get the most from lean programs.
Insights In Your Inbox
Subscribe to our Supply Chain Insights newsletter, sign up to receive Performance Improvement topic alerts and select other topics of interest to be delivered via email.
CHOOSE YOUR TOPICS
The industrial company that got bogged down trying to launch 30 tools eventually designed a new lean program refocused on the main causes of low equipment efficiency. Production line workers and shift supervisors adopted only four new behaviors: the use of real-time key performance indicators, discussion of production line performance at the beginning and end of every shift, better and faster root-cause analysis of problems and improved maintenance shutdown planning.
The key performance indicators, for example, showed that some crews were faster at getting the machinery up to target speed. Shift discussions revealed that the crew with the best time worked more as a team, helping one another as soon as they finished a task. The fastest crews then coached the others, accelerating machinery ramp-up time on every line.
New behaviors also helped speed root-cause analysis of production problems. If a machine broke down, the operations crew would meet the following morning and designate an owner to study the problem and propose a fix within a week. In the past, diagnosing the root cause of problems was a procedure that took weeks or months. The company’s revamped lean effort rapidly improved its overall equipment effectiveness: Within months, a majority of production lines showed significant gains, in best case up to 10 percentage points of OEE improvement.
Figuring out how work actually gets done and removing wasted steps and inefficiencies requires a bottom-up approach. But getting the best results takes a smart steer from the top.
Ilkka Leppävuori and Ives Moraes are members of Bain & Company's Performance Improvement practice. Ilkka is a partner based in Helsinki; Ives is a partner in São Paolo.
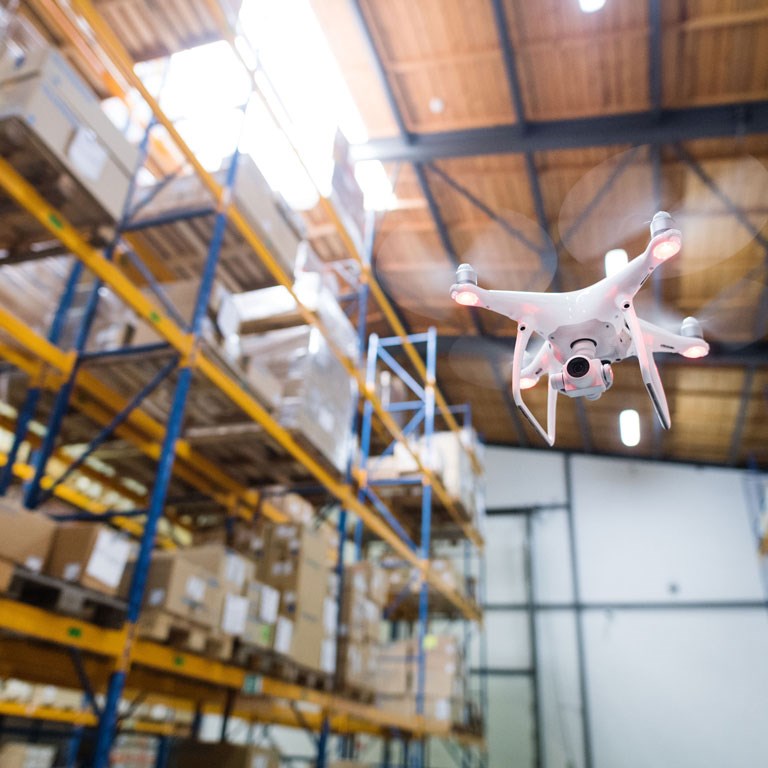
Operations Excellence
Companies with best-in-class operations have a strong competitive edge. Bain's insights on operational excellence help leadership teams transform supply chains, procurement strategy, and manufacturing capabilities into strategic weapons.