Global Machinery & Equipment Report
Резюме
- Supply chain executives are shifting investment priorities to reduce disruption and improve sustainability.
- Digital tools can help manage supply chain risks, improve efficiency, and measure environmental impact and cost in real time.
- Machinery companies are adding new capabilities, such as supply risk assessments and better network visibility, to bolster sustainability and resilience.
This article is part of Bain's Global Machinery & Equipment Report 2022
The new era of supply chain volatility has hit machinery and equipment makers especially hard. Over the past two years, a broad range of supply chain disruptions has battered the sector, from material shortages and price fluctuations to suppliers going bankrupt and, more recently, the devastating war in Ukraine.
At the same time, leadership teams are under pressure from consumers, shareholders, and governments to develop more sustainable machinery, trace raw material origins, and make their manufacturing processes transparent. In many countries, environmental regulators are raising the bar on compliance, and companies are being held accountable for not only their own environmental conduct, but that of their suppliers.
The solution to that dual challenge is resilient and sustainable supply chains. Our research shows supply chain executives across all industries started shifting future investments already in mid-2020 to focus on resilience and flexibility as opposed to cost reduction and speed (see Figure 1). For example, in response to the Covid-19 pandemic’s business disruptions, one technology company identified a series of investments to increase its supply chain resilience and flexibility. These included adding alternative suppliers for critical components and migrating up to 50% of its primary factory’s production volume to an additional manufacturing plant. The leadership team estimated these initiatives would cost about 0.5% of the company’s annual sales, a modest investment that could pay significant dividends during future supply disruptions.
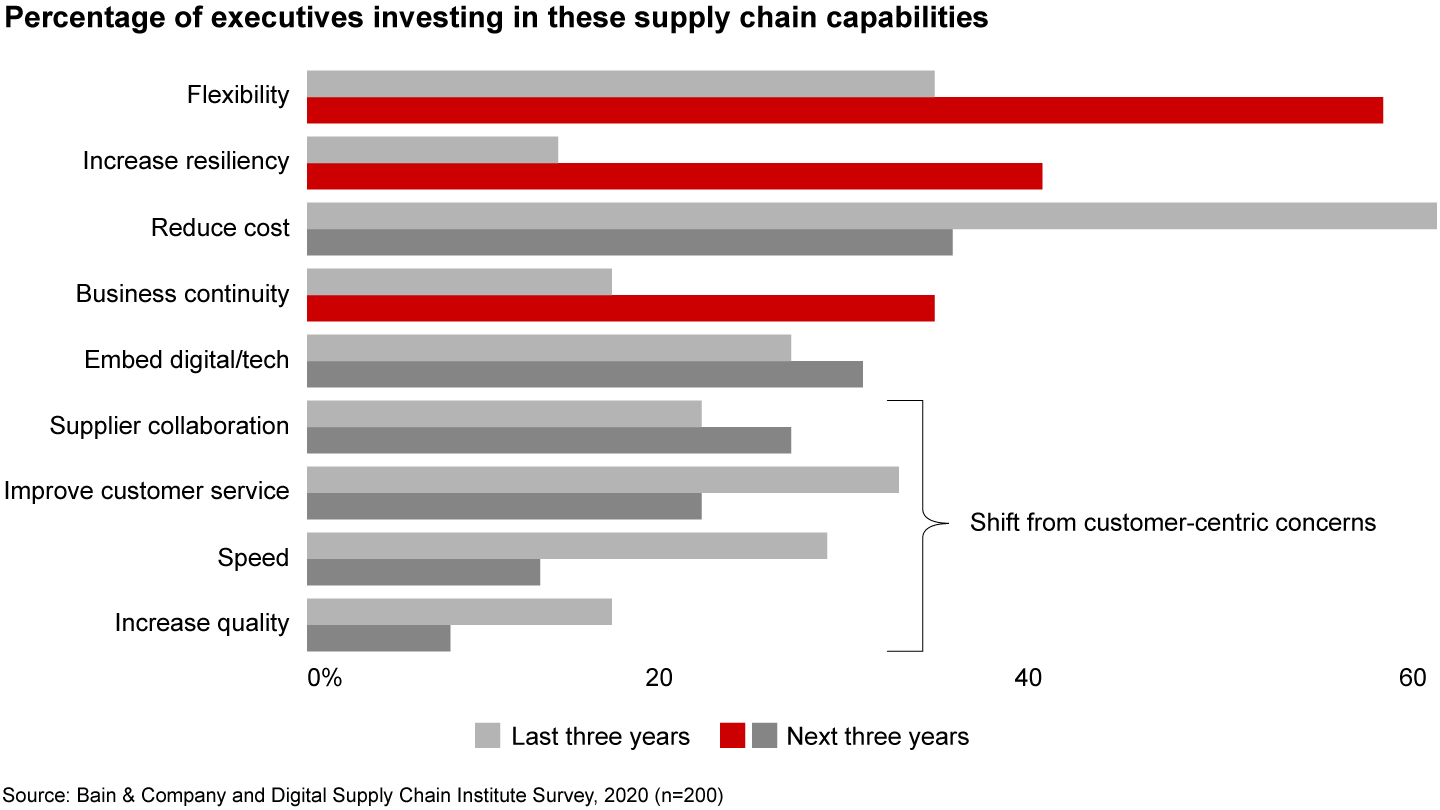

For machinery and equipment manufacturers, supply chain resilience has become an urgent objective over the last two years. Many were unprepared for rising material prices and supply chain disruptions leading to shortages of parts and components, and that was before the war in Ukraine caused additional global uncertainty and pushed material costs even higher. As a result, leadership teams have only just begun to focus on resilience and flexibility.
The benefits are clear. A new generation of digital technologies, including analytics and automation, delivers cost savings and efficiency, but also the transparency needed for greater resilience and sustainability. Advanced analytics, for example, can improve supply chain forecast accuracy by up to 60%. Leading companies have begun wielding predictive tools such as cross-industry supply and demand analytics and supply chain risk scoring to bolster their resilience.
Digital tools also help companies significantly reduce environmental impact and cost. In 2019, Sandvik launched a sustainability assessment tool that measures its worldwide energy use and waste as part of a pledge to reduce energy use in operations by 2.5% a year through 2030. A constant stream of data tracks the company’s progress toward creating green and sustainable factories.
But building resilience and sustainability into operations goes far beyond an investment in digital tools. Both objectives increase strategic and operational complexity. Until recently, most companies have managed supply chains as cost centers focused primarily on efficiency. Now, to mitigate more frequent disruptions and address sustainability, leadership teams need to rethink their supply chain priorities. That’s one reason why many machinery companies remain stuck in the early stages of transforming their supply chains.
New capabilities
To improve supply chain sustainability and resilience, operations managers must continually assess trade-offs with efficiency in an ever-changing economic landscape. As a result, machinery companies need to develop new capabilities—and quickly. Supply risk assessment, for example, helps ensure an organization dedicates the resources and expertise to track industry-level risks to vital inputs. It includes monitoring global supply and demand dynamics as well as macroeconomic and geopolitical risks. In tandem, resilient organizations continually assess the strategic risks linked to Tier-1 suppliers and their suppliers. Risk experts codify best practice and communicate it throughout the company.
Another key capability is network visibility. Companies with the most transparent supply chains incorporate suppliers and their suppliers in an extended value chain. That involves integrating customers into enterprise resource planning systems and sales and operations processes. Transparency leaders also share long-term strategic and production plans with their suppliers and establish joint product roadmaps. Such collaboration gives companies significantly greater ability to assess the capabilities of their Tier-2 and Tier-3 suppliers. Ultimately, improved visibility not only increases supply chain resilience; it can also help companies track carbon emissions and environmental impact.
Finally, resilient and sustainable supply chains depend on internal collaboration across functions. Leaders redesign the operating model to improve internal cooperation between business units. They ensure that procurement heads and supply chain managers provide regular input to sales, R&D, and strategy teams on supplier choice and sourcing strategies. That helps manage risk and ensure cost reduction efforts don’t undercut resilience.
Once these critical capabilities are in place, leading companies focus their investments in three key areas to rapidly bolster resilience and sustainability—prediction, flexibility, and circularity.
Prediction
Digital technology has dramatically improved the ability of companies to predict disruptions, delivery times, customer demand, and prices. Scenario planning, based on data collected from sensors and connected equipment, allows companies to anticipate internal disruptions and implement mitigation plans before supply shortages hit.
Companies with strong predictive capabilities use a predictive risk assessment framework to identify and prioritize supply chain threats across every dimension including those related to commodity shortages, geopolitics, and sustainability issues. The key challenge is making sure the assessment is dynamic, so it flags when a future risk moves from moderate to imminent, for example.
Toyota’s efforts over the past decade to improve supply chain transparency, risk assessment, and resilience highlight what machinery companies can learn from other industries. In a major break with its own organizational culture, the company replaced its vaunted just-in-time production system with a hybrid model that includes stockpiling 300 critical components and diversifying the supplier base. It also implemented a “rescue” tracking system for vulnerable components and suppliers and set up teams to monitor and manage supply chain risk. Finally, the company renegotiated contracts to ensure suppliers prioritized Toyota’s orders. The company’s long-term strategy to improve supply chain predictability and increase resilience has paid big dividends. While not immune to production delays during the recent global semiconductor shortage, Toyota has performed better than many automakers.
Machinery companies also are bolstering their ability to identify supply chain threats before they disrupt production. Following the Fukushima earthquake and nuclear disaster, Daikin, a global maker of air conditioning and refrigeration machinery, invested in analytics software to automatically forecast supply and demand. The tandem between manual forecasting and automated predictions allows both the algorithms and supply chain managers to learn from each other and continually improve supply chain performance. Daikin’s digital system has enabled the company to generate one statistical forecast for an entire region instead of relying on multiple local forecasts.
Leadership teams can improve the organization’s prediction capabilities by adopting cross-functional ways of working in all areas related to the supply chain, and by creating seamless connections with suppliers. That approach leads to greater transparency and efficient communication across silos. At the same time, leaders ensure the organization has the right talent and expertise to manage supply chain risk. Finally, they create dedicated resiliency teams to oversee inputs, analyze results, and prioritize risks.
While prediction is critical, companies won’t always be able to anticipate external shocks. As a result, it’s just as important to build the ability to withstand or absorb sudden unexpected disruptions. Companies can prepare for external shocks by building redundancy into the supply chain—double sourcing vital inputs and producing the same product at different facilities. That allows companies to bounce back from disruptions faster than the competition.
Flexibility
Many machinery makers have long customized their product specifications to meet customers’ particular needs. That practice has, over time, led to a high degree of product variation, which in turn creates greater supply chain complexity, reduced flexibility, and higher costs. Companies can improve flexibility through changes to product design and manufacturing. Platform concepts that allow machinery companies to share common parts across a portfolio of products—much like automotive platforms for different car models—help streamline the total number of parts and reduce supply chain complexity, enabling companies to react faster. As supply volatility increases, leading manufacturers are moving from a “just-in-time” operations management to a “just-in-case” approach that builds more flexibility into the system. Machinery companies embracing a platform approach to design include Caterpillar, CNH Industrial, Komatsu, AGCO, and Wärtsilä.
As supply volatility increases, leading manufacturers are moving from a “just-in-time” operations management to a “just-in-case” approach that builds more flexibility into the system.
Digital platforms that help manage operations can significantly increase supply chain flexibility by enabling companies to react to changes almost instantly. Schneider Electric’s cloud-based Industry 4.0 platform, EcoStruxure Plant Advisor, supports real-time data exchange, tackling the problem of siloed data. The platform acts as the central node that connects a company’s factories, equipment, and vehicles, and delivers information across a network of sites globally. Digital connectivity creates smart supply chains that are more agile and more efficient. The platform, which Schneider first designed for its own plants, typically reduces unplanned downtime and input costs and boosts EBIT earnings by 6% to 11%.
Many companies are also reevaluating the degree of vertical integration that makes sense in a more turbulent global economy. In cases of extreme supply volatility, it may no longer make sense to outsource vital inputs. Tesla offers another example from the auto sector with lessons for all manufacturers. The company’s decision to invest in modular technology architecture and in-house Agile software development capabilities allowed it to avoid painful production delays triggered by the global semiconductor shortage. When microcontroller units (MCUs) grew scarce, Tesla rapidly developed and validated 19 new, alternative MCUs, while simultaneously developing firmware for new chips made by new suppliers. In 2021, Tesla outpaced every auto plant in North America in production volume and gained market share.
Circularity
As customers, governments, and investors demand cleaner, more efficient, and sustainable machines, leading OEMs are developing circular supply chains that reduce waste, recycle materials, and make operations more energy efficient. Factory-based changes that support circularity include designing more durable products and machinery that can be adapted for multiple uses.
ABB, for example, has joined an industry-wide forum for Swedish companies to increase the circular flow of materials with a special focus on electrical products. In 2020 it entered a two-year collaboration with Swedish paper and pulp company SCA to improve the efficiency of its equipment by installing smart sensors on all SCA’s electric motors. The sensors relay information about each motor’s operation and health over a Bluetooth gateway or smartphone to a secure server. ABB is also recycling and replacing older motors with more energy efficient models. And in collaboration with Stena Recycling, the company is working to recycle and reuse all material residues of iron copper aluminum and other raw materials.
Elevator maker Kone has achieved big gains in resource efficiency and the use of sustainable materials. The company now recycles 90% of metals and other materials in its products and 94% of waste is recycled or incinerated. Modernizing its elevators has generated up to 70% in energy savings. The company also has set a goal of zero waste to landfill by 2030. Artificial intelligence, robotics, and green energy were key to optimizing manufacturing material and improving energy efficiency.
Companies can also achieve circularity gains outside the factory. One key step is building traceability into the full value chain. Tracing materials is a prerequisite for feeding them back into the conversion process for reuse, recycling, or remanufacturing. Leading machinery makers are working with suppliers upstream to check the C02 balance of raw materials, minimize waste, and improve product sustainability.
John Deere, for example, has engaged EcoVadis to assess the sustainability performance of 400 key logistics and material suppliers in an effort to reduce the environmental impact of its products. The company plans to extend that process to more than 1,000 suppliers (60% of material spending) by the end of fiscal year 2022.
Circular design can also improve a product’s sustainability. In the machinery sector, circular design increases the use of reusable, renewable, recycled, or refurbished materials. John Deere has launched life-cycle assessments to measure the environmental footprint of its products and has pledged to recycle 85% of total waste by the end of 2022. The company also is increasing its use of sustainable materials and aims to generate 30% of sales from rebuilt and remanufactured products by the end of 2022. In 2020, for example, John Deere started selling soy-based foam seats for tractors, which it developed in-house.
The global shortage of raw materials and key commodities including rare earths is also increasing pressure on machinery companies to embrace circularity. One option is to reuse materials, reducing production impact on the environment and improving supply chain resilience. Hitachi Construction Machinery Group has begun remanufacturing parts for construction machinery to improve resource efficiency. The group’s remanufacturing business, which reworks old parts to have the same performance as a new one, reduces waste by about 2,900 metric tons per year. Automaker Tesla and others are working to bend the cost curve on extracting nickel and cobalt from lithium-ion batteries. And some companies are redesigning products to decrease dependence on certain materials or avoid using them altogether.
Prediction, flexibility, and circularity are vital capabilities in adapting to a more volatile economic landscape. Of course, these are not the only factors that contribute to resilience and sustainability. A shift in the mindset among workers throughout the organization, a governance structure to uphold ethical standards, and other risk policies are important. However, tackling prediction, flexibility, and circularity first will help companies accelerate the shift.
Machinery companies face a step change in operations. The traditional approach to managing networks, which helped companies remain competitive for decades, won’t work going forward. Growing global pressure for sustainable products and processes will create an entirely new set of rules for managing operations. To succeed, leadership teams will need a more holistic view of the market, dramatically improved supply chain visibility, and sustainable products and processes.
Machinery companies face a step change in operations. The traditional approach to managing networks, which helped companies remain competitive for decades, won’t work going forward.
Companies on the forefront of the shift toward resilient and sustainable supply chains have a head start building competitive advantage in the markets of 2030 and beyond. They will bounce back faster in times of supply disruption and benefit from a tailwind of support from customers, investors, and regulators.