Management Tools
What Is Lean Six Sigma?
Lean Six Sigma is an approach to project management that combines elements of both Lean Manufacturing and Six Sigma approaches. Lean Six Sigma originally was designed to improve manufacturing quality to no more than 3.4 defects per million opportunities. The combination of Lean and Six Sigma helps companies achieve higher quality in a fast and efficient way by creating a culture of responsiveness and accountability. Lean Six Sigma programs constantly measure and analyze data on the variables in any process, and then use statistical techniques to understand what improvements will reduce defects and improve efficiency. Such programs also incorporate a strong system for gathering customer feedback. Companies have applied Lean Six Sigma to functions ranging from manufacturing to call centers to collections.
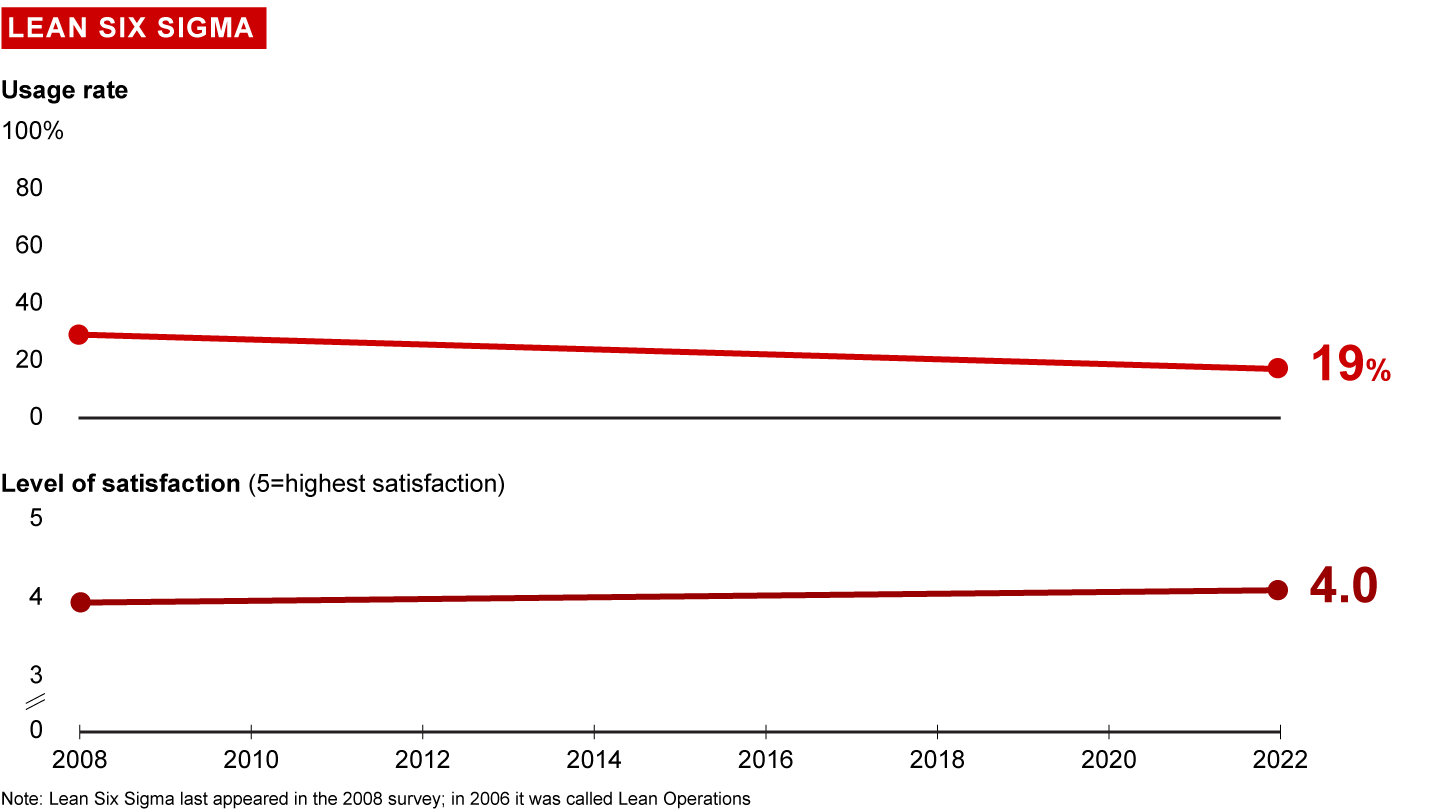

How Is Lean Six Sigma Implemented?
Prior to using Lean Six Sigma, companies should deploy an upfront diagnostic to identify the most critical opportunities. Then, Lean Six Sigma teams follow five problem-solving steps to quickly identify root problem causes, develop solutions, and implement procedures that maintain those solutions.
- Define: Identify the customer requirements, clarify the problem, and set goals.
- Measure: Select what needs to be measured, identify information sources, and gather data.
- Analyze: Develop hypotheses, and identify the key variables and root causes.
- Improve: Generate solutions, and put them into action, either by modifying existing processes or by developing new ones. Quantify costs and benefits.
- Control: Develop monitoring processes for continued high-quality performance.
Related Topics
What Are the Common Uses for Lean Six Sigma?
Companies use Lean Six Sigma to set performance goals for the entire organization and to mobilize teams and individuals to achieve dramatic improvements in existing processes. More specifically, Lean Six Sigma can:
- Make processes more rigorous and efficient by using hard, timely data to make operating decisions
- Cultivate customer loyalty by delivering superior value
- Accustom managers to operating in a fast-moving internal business environment that mirrors marketplace conditions
- Achieve quantum leaps in product performance
- Reduce variation in service processes, such as time from order to delivery
- Improve financial performance through cost savings, increased revenue, and expanded operating margins.

Management Tools & Trends 2023
On the 30th anniversary of our survey, managers seem surprisingly upbeat.