Article
Резюме
- The economic fallout of the Covid-19 pandemic will constrain capital investment in most energy and natural resource companies.
- Some investments still make sense, like event-driven monitoring, which allows companies to ensure their equipment is reliable, relying on fewer people to do the monitoring.
- Event-driven reliability makes use of existing technologies and systems to guard against failure and lost production. The data can also help businesses prioritize which pieces of equipment should be taken offline for maintenance.
The Covid-19 pandemic has touched billions of people around the world and brought millions of businesses to a virtual standstill. Many business leaders, who were already concerned about their abilities to care for their people, are now also trying to determine how to endure the economic shocks that are sure to follow in the pandemic’s wake. Many are reviewing investment plans, including programs to digitally transform their operations. While some more elaborate programs should pause, others deliver quickly on reasonable investments.

Macro Surveillance Platform
For more detail on the business implications of coronavirus from Bain’s Macro Trends Group, log on to the Macro Surveillance Platform. Learn more about the platform >
One of these is event-driven reliability, a stepping-stone toward predictive maintenance that helps companies digitally monitor their assets and guard against the risk of failure and lost production. Event-driven reliability taps existing process controls and sensors (for example, temperature, flow rate and pressure) across disparate information sources to determine whether equipment is operating outside of normal conditions (see Figure 1). It builds off traditional condition-based monitoring by using advanced analytics and new workflow tools to generate real-time, targeted insights about future performance. Abnormal conditions trigger events like an automated action (for example, sending out a work request or stopping a process) or a notification to an expert who can decide what action to take.


Done right, event-driven reliability is fast to implement, making use of the installed base of sensors to improve safety and reduce the need for staff in the field. It can also reduce your maintenance operating expenses, which can account for 25% to 35% of operating expenses.
Fewer people, lower risk, faster value
The ability of businesses to continue to operate with fewer people on site will be important in the months and years ahead. One North American mining company was able to quickly set up monitoring of more than 100 kilometers of critical underground conveyor belts, simplifying a task that had been performed either through manual inspection or by teams reviewing reports after the fact, sometimes a few weeks later. After an implementation period of four weeks, an event-driven reliability system now monitors the entire system twice a second, looking for events that indicate a potential failure. In the first month online, the company avoided about 20 hours of downtime that might otherwise have occurred, and over the first four months detected more than 30 potential downtime events with no false positives.
In addition to guarding against imminent failure, a continuous feed of asset information also informs decisions about risk levels, allowing operations and maintenance teams to make critical decisions balancing production and reliability. One chemicals manufacturer used a risk assessment to determine which pieces of major equipment posed a higher risk of failure, and so should be taken offline for service, while others were allowed to operate on full during high-demand periods.
These systems also allow engineers to monitor activity remotely, even from home. One oil and gas company saved $8 million over six months by remotely monitoring oil well temperatures, which reduced unnecessary inspections and truck rolls by 18%.
Getting it done right
In many plants and other assets, the information necessary to keep things running smoothly resides in the heads of engineers and managers who may have worked on-site for decades. Setting up an event-based reliability system captures and codifies this knowledge, creating opportunities to revisit existing maintenance strategies that may not have been reviewed or optimized in years. Relieving experts of the burden of monitoring systems can free up time that could instead be invested in optimizing operational and maintenance processes.
Successful implementations deliver quickly on the investment by adhering to four key principles.
- Identify improvements that will deliver the most value. Often, managers and engineers focus on opportunities that are easily accessible or deliver quick wins in areas of high visibility. Most need to dig deeper to gain a better understanding of which digital investments offer the potential to generate the greatest value across operations.
- Close feedback loops. Track feedback to continuously improve the quality, accuracy and effectiveness of events.
- Design solutions to be integrated with operations. Technology isn’t the critical constraint; it’s designing solutions that are easy to operationalize—that is, solutions that are prewired to the maintenance and work management processes, and so will be easy to implement and be quicker for people to learn.
- Proceed as with stepping-stones. Build fast and small, gain early successes and demonstrate value to win supporters. Think of each step as part of a longer journey, crossing from one side to the other. Balance completeness with complexity.
In the years ahead, industrial companies will develop more comprehensive predictive maintenance systems. Until then, there’s a long tail of opportunities, monitoring systems and identifying patterns that suggest risk, and digital, event-driven reliability systems can help them do that affordably. Investing in these systems today can help companies build in resilience that helps them weather the turbulent period we are just entering.
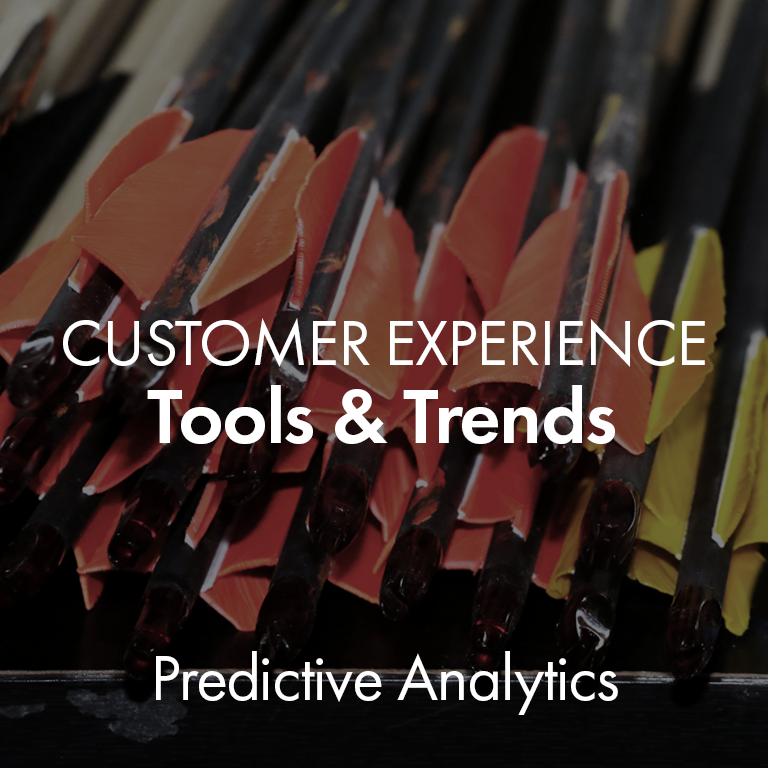
Predictive Analytics
Understanding the likely next steps of a potential buyer helps companies improve their customer experience, increase loyalty and build value for the organization.

Coronavirus
The global Covid-19 pandemic has extracted a terrible human toll and spurred sweeping changes in the world economy. Across industries, executives have begun reassessing their strategies and repositioning their companies to thrive now and in the world beyond coronavirus.