Brief
Резюме
- Companies that reassess engineering support on mature programs can increase profitability by up to 200 basis points.
- Adjusting the level of engineering support on mature programs allows companies to redeploy staff to critical development programs.
- Several red flags, including multiple technical changes, may signal overengineering on mature programs.
The holy grail in defense has always been to reach production maturity, since that’s when programs generate maximum cash flow and profit. The irony is that programs in this phase often perform below full potential and maintain technical support levels that are higher than necessary.
Most companies tend to overlook the efficiency of mature programs precisely because they are delivering high volumes, high revenue, and high margins.
Leading companies reassess the level of engineering support staff needed for mature programs and redeploy those resources to other critical areas. That approach produces multiple benefits and a substantial return on investment (ROI). Profitable programs generate even higher margins—often a gain of 100–200 basis points. These companies also achieve a 10%–15% reduction in engineering hours on mature programs (see Figure 1). That enables management to shift scarce technical talent to development programs and proposals that are critical to future growth. Finally, improving engineering efficiency reduces unit costs, decreasing the risk that government agencies will reduce funding or even cancel programs.
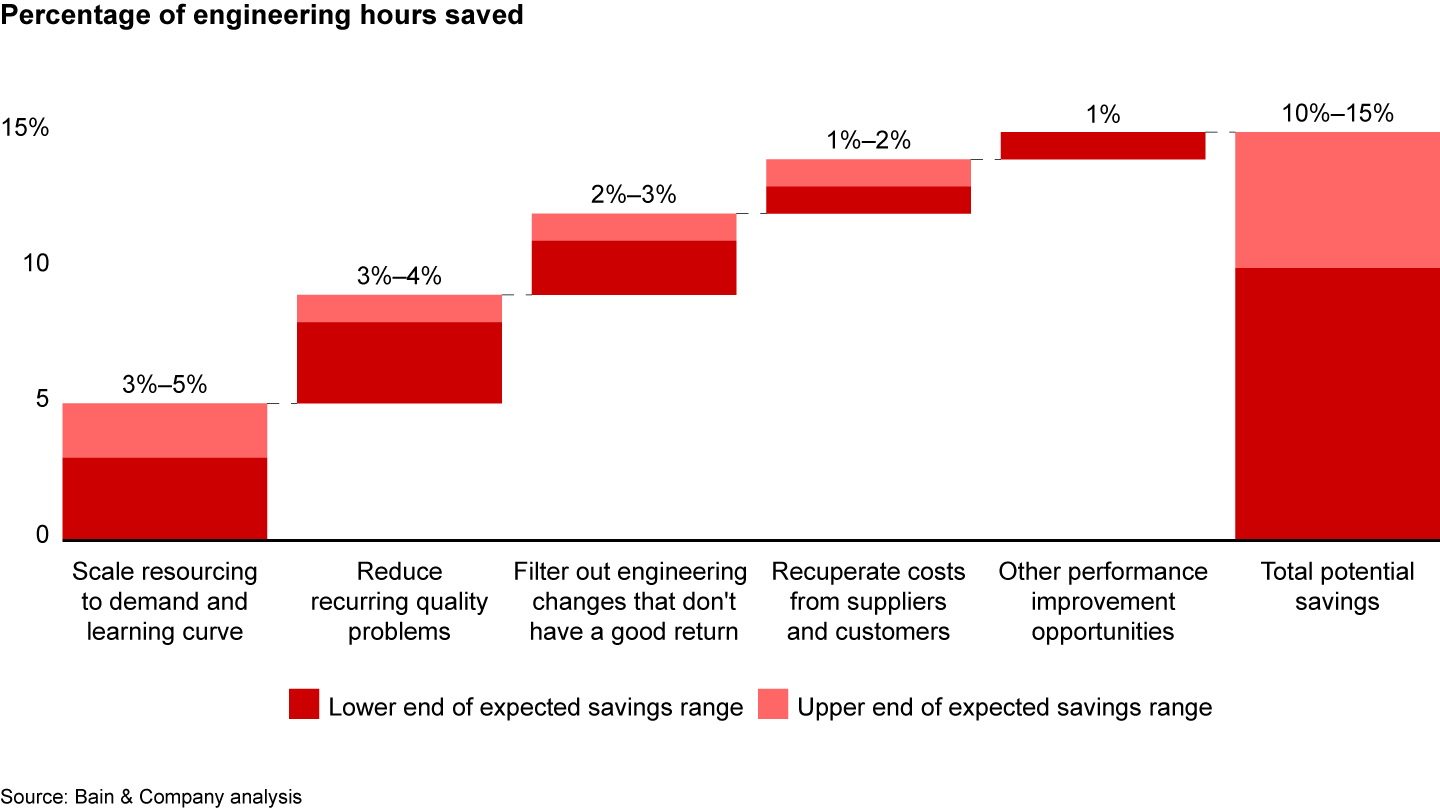

Companies can identify potential efficiency gains in their mature program portfolio by looking for several key indicators of overstaffing:
- No change over time in the number of engineering staff supporting production and sustainment work. Learning-curve efficiencies should enable a steady decrease in engineering resources.
- Recurring quality problems linked to internal processes or suppliers. Often, recurring problems occur when engineers implement a quick one-time fix to meet delivery pressures instead of resolving the root cause. As a result, engineering resource levels remain high since the team is forced to address the same problem over and over.
- A large volume of engineering changes, particularly elective changes such as those that improve manufacturability but have a questionable or undefined ROI. The modifications may be well-intentioned, but often are not worth the investment.
- Significant levels of incomplete work passed to the next stage of production, out of sequence, due to unresolved quality issues.
- Consistent cost overruns.
Companies with highly efficient mature programs follow three key guidelines:
Scale resourcing to meet demand. Leading companies adjust engineering resources in mature programs to an appropriate level. Of course, staffing levels should reflect demand factors, such as the production rate. One effective approach is to apply resourcing mandates, such as a 3%–5% reduction in resourcing per year for comparable work to ensure the organization takes advantage of learning curve efficiencies. On a typical program, each 5% reduction in engineering support on mature programs can free up 10 to 15 engineers. One aerospace company reduced the level of engineering support for production and sustainment work by one-third, based on learning curve efficiencies and production rate changes. Best-in-class companies also reduce staffing buffers (added staff for just-in-case scenarios) and identify areas where they are overdelivering on contractual requirements. If they are overdelivering, they stop work or require reimbursement.
Reduce recurring quality issues. Repeated quality work-arounds demand significant engineering resources. Take the case of a product that fails to meet a specification. Instead of fixing the root cause, companies often send the product back to engineering for a one-time fix or a “use-as-is” disposition in order to keep production lines flowing. Often, the most effective way to address recurring quality issues is a permanent fix as opposed to quality work-arounds. One defense company analysis revealed that nearly half of the quality issues on a mature program occurred more than five times, and nearly a quarter of them occurred more than 10 times. Identifying the root cause of these issues and putting permanent solutions in place freed up 10% of total engineering support on the program.
In addition to eradicating internal quality problems at the source, leading aerospace and defense companies also target external inefficiencies. They work with customers to modify unnecessary specifications that create costly recurring work. They require suppliers to apply the same root-cause approach to eliminating quality problems. And if supplier quality problems necessitate work-arounds, they bill suppliers for the added cost.
Filter out engineering changes that don’t have a good return. Some technical changes to a part may save a few minutes of production time but simultaneously make a warehouse full of parts obsolete. Make sure each engineering change has a positive ROI after the full cost of implementing the change throughout the value chain. One helpful step is to require a preliminary business case review of any proposed internal engineering change. And when customers request technical changes, ensure that they cover the cost.
Take the case of a global helicopter company that increased the efficiency of its mature programs significantly by winnowing out unnecessary technical changes. Before approving such changes, the leadership team required managers to assess the total expected cost and return in all functions including engineering, supply chain, production, and the aftermarket. That approach reduced internally generated changes by about 50% within six months, freeing a team of engineers to work on a critical new development program.
It’s easy to overlook efficiency gains in aerospace and defense programs that are generating relatively high returns. But as companies grapple with a severe shortage of technical talent and pressure on margins, leaders are taking a harder look at the programs they once viewed as the stars, only to discover they operate well below their full potential. That’s a rare opportunity to boost performance.