Brief

A series of disruptions has reduced the global supply of plastic resins, the ubiquitous building blocks used to make the soda bottles we drink from, the fibers in our athletic clothing, the personal protective equipment that medical providers rely on, and the dashboards in our cars. These disruptions included a perfect storm of supply factors—severe weather in the US, unplanned production outages, and a global shortage of shipping containers. At the same time, surging demand and rising oil prices triggered a dramatic increase in resin prices beginning in early 2020.
The prices of the two most common resin types, polypropylene and polyethylene, rose 180% and 125%, respectively, in the US. In Europe, despite the broader supply base, prices for the two resin types increased by 67% and 77%, while in Asia they rose 25% and 30% (see Figure 1). Prices are only now starting to decline after peaking in August of this year.
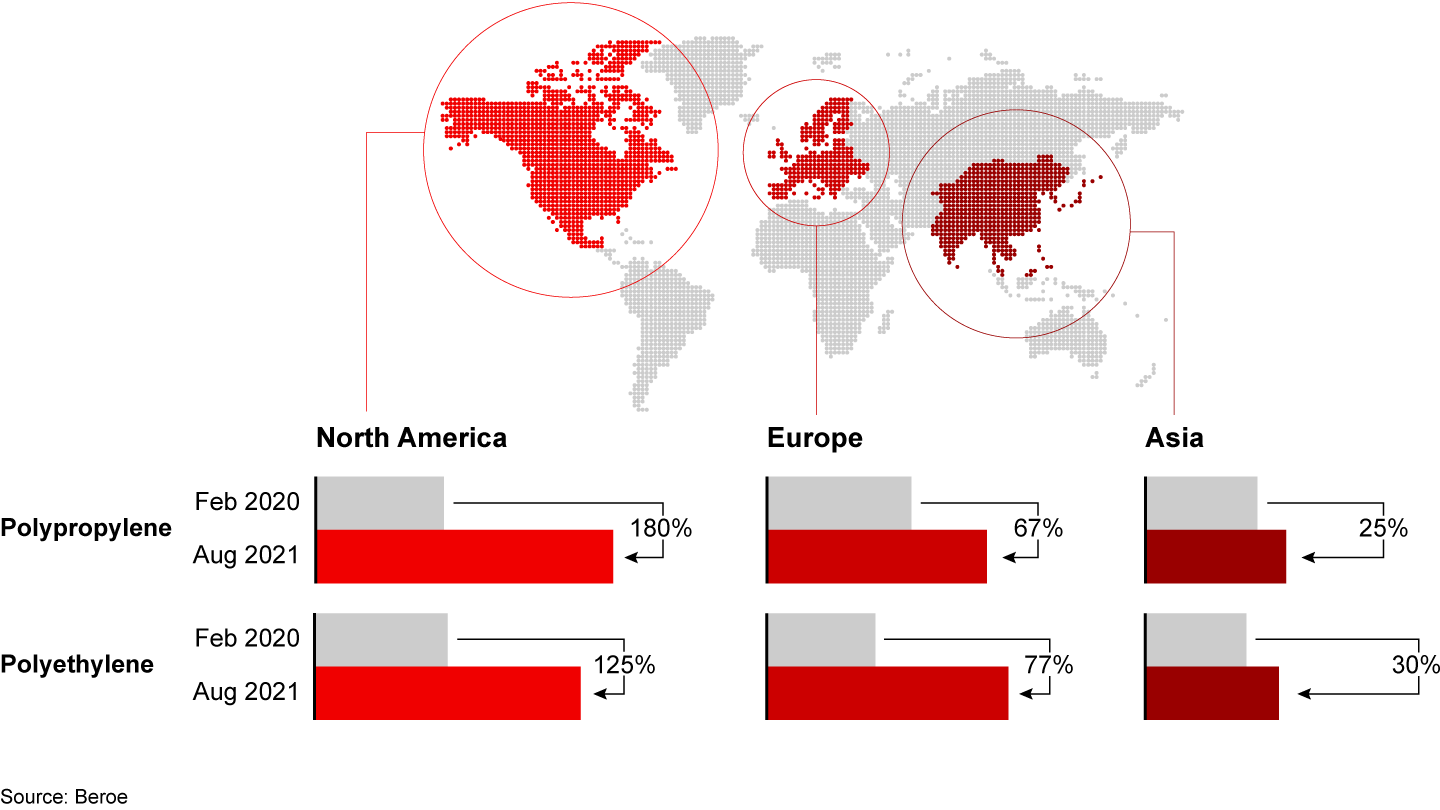
Those price spikes hold long-term lessons for companies that manufacture a variety of inputs, not just resins. In an era of heightened trade uncertainties, logistics challenges, and other disruptions, leading companies are taking steps to improve supply chain visibility and resilience and to more closely monitor supply and pricing risks. Companies can increase their resilience by qualifying alternate resin suppliers, identifying less expensive substitute materials, and adopting standard resin grades that make it easier to shift supply between alternative sources.
In 2022, the global imbalance between resin supply and demand should start to improve as most of the installed production capacity comes back online and demand for personal protective gear and takeout and grocery food packaging declines. These factors already have helped relieve some of the inflationary pressure on resin pricing, but it is unlikely that prices will return to prepandemic levels in the next 12 months.
Even as resin prices ease, leading companies are bracing for the next disruption, harnessing the procurement function to reduce costs and enhance supply chain resilience. Many are launching companywide cost transformations with renewed focus on cost reduction, including design-to-cost, simplification, and standardization across the procurement portfolio. At the center of the effort, procurement organizations are strengthening cooperation with internal business functions such as R&D, sales and marketing, and operations. They are also targeting more cost and supply chain transparency, mapping their suppliers to multiple tiers, and asking vendors for increased visibility on cost inputs.
Companies with best-practice procurement functions have a deep understanding of the factors that affect their supply categories. They achieve this by setting up permanent task forces with suppliers, mapping sources along the supply chain, and implementing automatic triggers to raise safety stocks when supply is at risk.
Painful spikes in resin prices have taught leadership teams important lessons about supply chain resilience and transparency. Companies that improve their understanding of supply categories and monitor supply and price risks closely will be in a stronger position the next time disruption strikes.