Brief
한눈에 보기
- Building construction contributes significantly to global greenhouse gas emissions and use of resources.
- Recycling and reusing building materials—that is, improving circularity—can help provide the residential and commercial buildings needed for a growing population while minimizing environmental impacts.
- Europe’s construction sector is further along on the path to circularity, prompted by regulations that require recycling and reuse of materials.
- The shift represents a big opportunity for building material providers who are innovating many new lightweight and low-carbon substitutes for traditional materials.
Building construction is a significant contributor to the world’s emissions and materials footprints, accounting for about 40% of each. Most emissions associated with buildings result from their operations—primarily heating and cooling. But the embedded emissions in building materials still account for 28% of construction-related emissions.
Improving circularity in construction will be necessary to reduce the sector’s emissions and materials footprint. It’s a global challenge, and particularly critical in regions experiencing rapid population growth and urban migration, which generates significant demand for new construction. In this brief, we look closely at the European buildings sector, where regulation has helped push the industry to become more circular, focusing on end-of-life materials recycling and recovery.
While emissions reduction efforts will understandably focus on low-carbon technologies such as green steel and CO2-injected concrete, to deliver against net-zero goals the industry will also need to reduce the need for virgin, raw materials.
One way to reduce the demand for virgin materials is to ensure the best use of end-of-life materials—that is, material that can be reused or recycled when buildings are renovated or deconstructed. Because these materials are scarce (particularly in Europe, where buildings have long lives), the sector is also developing innovative new materials and working to secure access to recycled materials from other sectors.
In this brief, we describe five tactical strategies that companies are making to improve their circularity, and we share three principles that they are using to navigate the shift to a more circular construction industry.
Europe’s progress on circularity in construction
In Europe, policy and regulation have played an important role in encouraging the construction sector to become more circular, especially the European Union’s Waste Framework Directive, the 2008 version of which aimed to have 70% of construction and demolition waste recycled by 2020.
Today, Europe’s construction sector, including light industrial, commercial, and residential (not infrastructure), is about 30% circular, with the potential to reach 50% by 2040 (see Figure 1). (We calculate circularity as the weighted average of the percentage of material inflows and material outflows, per the Circular Transition Indicator Methodology of the World Business Council for Sustainable Development.) Heavy materials, such as concrete and plaster, make up most of the material used in the sector. The current amount of recycled inputs is still very low. Concrete, for example, accounting for the highest volume, has only 12% recycled input.
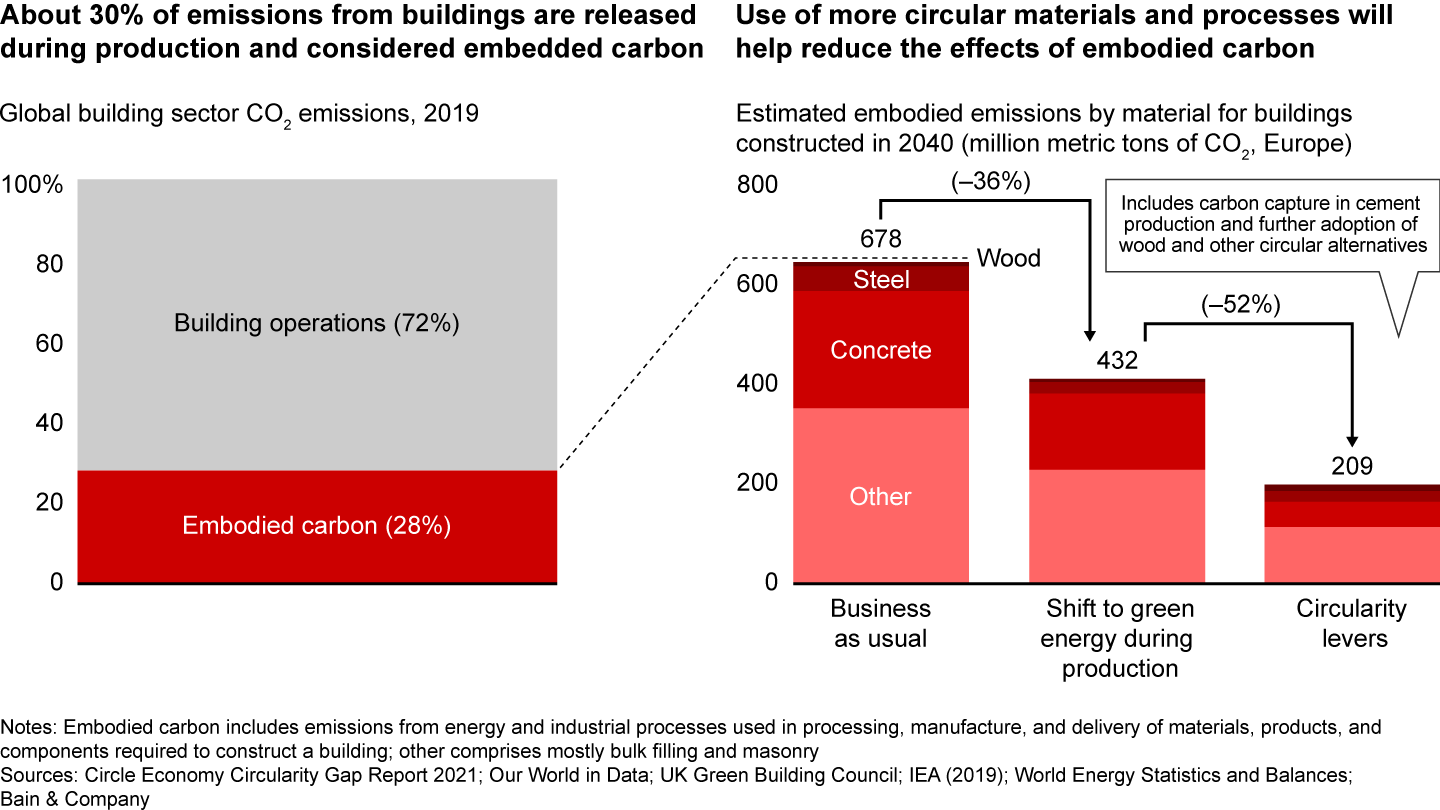

The shift to greater circularity will have a disruptive effect on the industry, especially on the makers of construction materials. Most of these companies are setting goals and putting pilot programs in place to explore ways to make the sector more circular. Owens Corning, for example, aims to deliver zero waste to the landfill by 2030, and Swiss building materials maker Holcim aims to double the ratio of recycled products in its product portfolio over the same period.
The pressure on these incumbents comes not only from regulators and customers. New entrants are also finding footholds in alternative materials and new services and business models. Incumbent leaders should be eyeing these disrupters carefully.
Biomason, for example, is a US company developing new types of cement using biotechnology. The company says their biocement takes inspiration from the formation of coral and other life forms that build with carbon building blocks. Their first commercially available product consists of about 85% granite from recycled sources and 15% biocement, creating a precast that matches the strength and durability properties of standard materials with a much lower carbon footprint.
Another good example is ZenRobotics, a Finnish recycling company recently acquired by Terex Materials Processing of Northern Ireland, which uses artificial intelligence and robotic pickers to improve sorting for different types of waste streams, including construction and demolition.
Five circular strategies
The shift to circularity is transforming the ways that building materials are developed and used in the construction industry. Each strategy on its own has a limited impact on circularity and emissions reduction, but together they can deliver huge improvements. Bain’s analysis finds that if the industry’s circularity rises from 30% to 50% by 2040, this would cut the production-related greenhouse gas (GHG) emissions in half, in addition to significant gains achieved by shifting to green energy during production.
A 50% circular industry by 2040 could meet rising demand for commercial and residential buildings with far fewer materials: The total material use could drop from its current 642 million metric tons to 590 million metric tons annually—a reduction of 8%.
- Renovation and longer utilization. Improving existing residential and commercial buildings to extend their lives and make them more sustainable could provide a significant boost to the circularity of the sector. Trends are already improving the use of the built environment, which reduces demand for new building materials. Within Europe, the amount of residential and commercial space renovated could double by 2030. Changing attitudes about remote and hybrid work, as well as office sharing, will reduce the amount of real estate that companies need per worker. This should lead to more efficient utilization of existing stock due to remote and hybrid work or better use of capacity due to office sharing.
- Lightweighting. Innovations in design and materials could decrease building weight by 20% and embodied carbon by up to 15% by 2040. Lightweight substitutes for concrete, for example, can be up to 30% lighter. Thoughtful design can also reduce weight by optimizing the type and amount of material used.
- Renewable inputs. The market for building materials made from renewable inputs is small but growing quickly. The use of cross-laminated timber (CLT), for example, is growing at about 13% annually, sequestering carbon while acting as a structural replacement for steel and concrete. Leko Labs is one company that makes sustainable, wood-based material, which it says is strong enough to replace up to 75% of concrete and steel within a building. Showcase projects such as the 10-story-tall Dalston Works in London—the world’s largest CLT building—are important for showing the capabilities of new materials.
- Circular inputs, from the construction industry and beyond. Increasing the amount of recycled content, with improved collection and recycling consistency, could help to almost double the share of recycled materials (to 28%) by 2040. Of that recycled content, only a quarter comes from the construction industry today; the rest comes from other industries. The demand for new construction globally, combined with the long life span of buildings, means that there are nowhere near enough building materials reaching end-of-life to satisfy the demand for construction and renovation activities. Recycled concrete is one promising example: Traditional crushers reduce concrete to pebbles that can be reused, but a new technique called SmartCrusher goes further, separating the concrete stone from other materials so it can be reused in new concrete, reducing the CO2 required to make new concrete.
- Recovery services and technology. Better management of waste during construction and demolition, including more advanced material separation techniques, can help increase the amount of materials to be reused or recycled. Some potential lies in better planning and transparency for recoverable materials that could become available in certain markets. By 2040, as much as 100% of construction and demolition waste could be recycled, and 49% (up from 18% in 2020) could be reused in construction. This could boost overall circularity by 3.6 percentage points and grow the market for these materials 1.5 times faster than the market for new construction. But given the long lives of buildings, design changes that make material easier to recover is likely to have a limited impact over the next 20 or 30 years.
Collectively, the building materials sector embracing these levers and strategies could increase circularity to 50% by 2040 (see Figure 2).
Navigating the transition to a more circular sector
Players in the global construction industry, and specifically building materials companies, should take a proactive approach to make the most of the shift to a low-carbon economy. Our experience working with companies in this sector suggests that the companies out in front are guided by three principles that help them navigate the transition.
- Anticipate the circular materials disruption. The shift to circular materials, driven by policies, regulations, and consumer demand, will disrupt the construction sector. By now, most building materials companies are positioning themselves to make the most of the opportunities, whether that’s through investments in new materials, technologies, or services. New disrupters are enabling transparent and predictable supply of end-of-life materials, which has the potential to fuel a new wave of circular materials disruption.
Madaster, for example, is a start-up that has created a new business model with an online registry of building materials used in construction projects. The Madaster Platform maintains a “materials passport” for every construction project included, containing information about the quality, origins, and location of materials used in buildings, to facilitate the salvage, recycling, and reuse of those materials at the end of the building’s useful life.
- Use circularity as a commercial selling point. Because greener and more circular materials can help customers reduce their own emissions, they offer savings that most customers should be willing to pay a premium for. But materials companies have not always priced their products appropriately to capture those premiums. By focusing on customer segments that place a high value on circularity benefits, and by quantifying the value delivered to customers, materials makers can determine the right price and margins. A clear understanding of the value to the customer will help sales teams articulate the circularity benefits.
Holcim sells a range of concrete materials under the ECOPact brand that produce 30% to 100% less emissions than traditional concrete and that integrate recycled construction and demolition materials—benefits that help their customers reduce their footprint. In many places, the demand for these materials far outstrips their potential supply. Getting the appropriate price is important to help grow the industry and accelerate the transition, which will further boost these businesses.
- Secure cost-competitive access to circular materials. Because buildings have such long lives, the volume of inputs needed for new construction far outweighs the volume of materials that can be salvaged from buildings at the end of their useful lives. As noted above, this means that the industry will need to draw on recycled materials from other sectors. But even with these, there is bound to be strong demand and competition for these materials (see Figure 3). Supply chain disruptions will only increase this challenge. Builders and makers of construction materials will want to secure access to end-of-life materials as early as they can, to avoid being left exposed to inflation and scarcity.
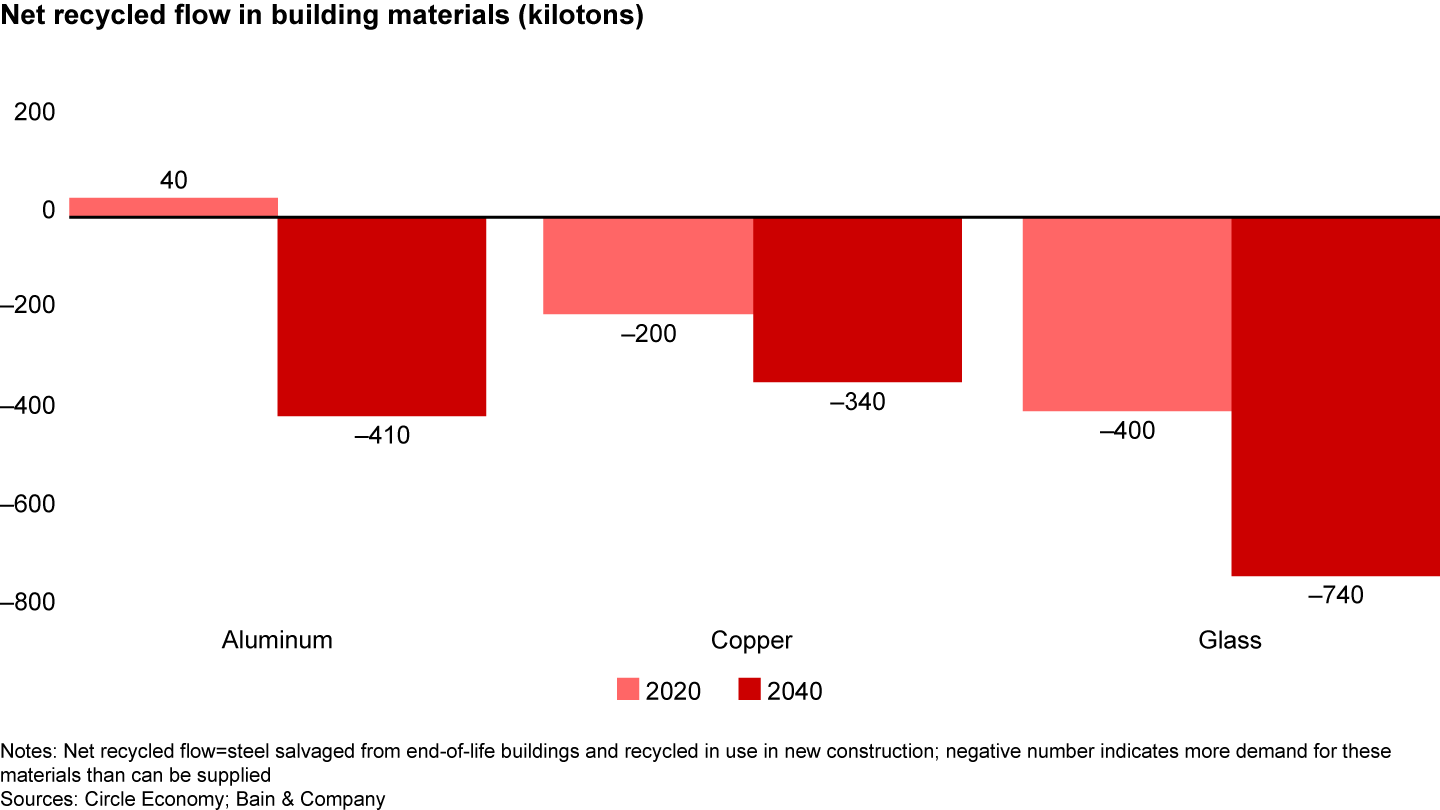

Historically, the construction industry has been slow to adopt new technologies and processes that deliver productivity gains. But that’s changing quickly: Construction and building technology are among the hottest draws for venture capital, and the industry is rapidly adopting digitization.
The same is true for sustainability and circularity. If you visited a construction site tomorrow, you might not see many signs of circularity. But much of the work is in development or already operational in pilot programs. Some construction leaders, particularly in Europe where they have been spurred to action by regulations, are already showing how to use less, emit less, and recycle and reuse more. However, since the industry comprises many small firms, broader change will take more time, requiring greater awareness, more training, and the right economic incentives.
Beyond that, the industry is also pushing forward new technologies and product innovations to boost sustainability in a broader context, thereby reducing the environmental footprint of buildings in general. For example, Velux, a manufacturing company that specializes in roof windows and skylights, produces rooftop windows with expanded functionality to capture rainwater and to adjust the amount of light entering a room. Not only does this support more sustainable ongoing operations, but it also reduces the load of air conditioners that need to be installed at the onset.
After many years, the construction industry is finally showing that it can become more tech savvy and greener.