Etude
En Bref
- Flexible supply networks help companies minimize the risk of disruption in times of stress.
- Investments in supply chain resilience can deliver a 15% to 25% improvement in plant output and a 20% to 30% rise in customer satisfaction, Bain’s experience shows.
- Advanced analytics can improve supply forecast accuracy by 20% to 60%.
It happened faster than anyone could imagine. As China sent workers home and shuttered businesses in January to contain the coronavirus outbreak, the steady flow of vital parts to global supply chains slowed or stopped. The unexpected disruption sent shock waves through boardrooms around the world, just as the Covid-19 pandemic began to spread.

Macro Surveillance Platform
For more detail on the business implications of coronavirus from Bain’s Macro Trends Group, log on to the Macro Surveillance Platform. Learn more about the platform >
Confronted with an unprecedented public health crisis, companies everywhere have rightly concentrated first on ensuring employee safety and supporting their local communities. Manufacturers in critical industries scrambled to find alternative suppliers to keep factories running. Now, as some regions move past the most acute phase of the pandemic and start to plan for recovery, leadership teams are taking a hard look at supply chain reliability and risk.
The Covid-19 outbreak isn’t an isolated event. Disruptions are increasing in frequency and magnitude, including geopolitical events, climate-related disasters and public health crises. Brexit and the US–China trade war are recent examples. For decades, low-cost supply and minimal inventory were the key tenets of supply chain management. But in an increasingly turbulent world, supply networks that are overly dependent on the lowest-cost supplier and minimal inventory levels can rapidly imperil the business (see Figure 1).

When US–China trade tensions flared last year, leading companies already started to rethink the cost of network risk and invest in more resilient supply chains. Flexible networks help companies adjust quickly in times of stress. They also help production teams pivot nimbly to meet changing market demand, a significant competitive edge.
Bain analysis shows that companies with resilient supply chains grow faster because they can move rapidly to meet customers’ needs when market demand shifts. They increase their perfect order rate by 20% to 40% and customer satisfaction by as much as 30%. Importantly, flexible supply chains cut costs and improve cash flow, in part through a 10% to 40% increase in inventory turns. Finally, leaders reduce disruption by building buffers throughout the supply network and invest in advanced analytics to improve planning and forecasting accuracy (see Figure 2).

Cost vs. resilience
Once the pandemic passes and the global economy begins to function normally, many senior executives might assume they should manage their global supply networks as in the past, with the lowest-cost supply and minimal inventory levels. While that approach worked in a stable global economy, it now brings increased risk. The assumptions about supply chain management have shifted.
Leadership teams that have suffered a sudden shortfall in raw materials or parts know how costly it can be. A global electronics manufacturer suffered a 16% drop in revenue and a 66% decrease in net income in 2016, when a series of earthquakes in Kumamoto, Japan, cut off the supply of parts. And for one global automaker dependent on parts produced in Thailand, the floods of 2011 resulted in a 5% drop in global output, equivalent to $5 billion in lost sales (see Figure 3).

Successful companies are investing in supply chain resilience to minimize those risks and to benefit from improved efficiencies. Take the example of Procter & Gamble, which deployed a cloud-based platform to provide real-time information on production and external demand to its supply chain control tower. That strategy helped minimize the fallout when Hurricane Sandy slammed into New Jersey in 2012, disrupting production at a factory producing 91% of its perfumes. Insights generated by advanced analytics helped the company make the right decisions quickly, limiting the plant’s downtime to 2½ days. Learning from that experience, P&G used digital tools to prepare for Hurricane Irma’s landfall in Florida in 2017 and predicted which suppliers, plants and distribution centers were likely to suffer damage. That allowed the company to prepare contingency plans and relocate inventory. As a result, the company avoided the disruption and financial loss other companies suffered.
Toyota also has invested in new capabilities to improve supply chain resilience. Working with its partners, the company created a database to visualize supply networks for each component. If disaster strikes, Toyota can immediately identify the parts at risk. The database identifies components that are supplied by only one manufacturer and are difficult to replace. The company then decreases dependence on solo providers by reducing the number of unique designs and sharing equipment specifications with parts production facilities and suppliers.
Competitive edge
In our experience, companies that invest in supply chain resilience reduce product development cycles by 40% to 60%. As production teams adjust faster to changes in market demand, revenue growth accelerates. Companies with flexible supply chains expand output capacity 15% to 25% by optimizing operations.
A global footwear maker, for instance, invested in a highly flexible supply chain that enables it to meet growing market demand for customization. Customers design one-of-a-kind shoes online, and the company delivers them in under 10 days. To achieve that speed, the company partnered with robotics and automation companies that can manufacture the bottom part of a shoe in 2.5 minutes, compared with 50 minutes previously.
The Covid-19 crisis has thrown a spotlight on companies that already have flexible production lines. The fashion industry couldn’t be further removed from the production of disinfectants and medical gear. But when the spread of Covid-19 overwhelmed the French and Italian healthcare system and medical supplies ran short, nimble luxury goods manufacturers overhauled operations to make the urgently needed items. Within 72 hours of the French government’s call for business to pitch in, LVMH’s perfume factories were producing hand sanitizer. Giorgio Armani, Gucci and Prada repurposed their designer clothing factories in Italy to churn out medical overalls, and Burberry harnessed a trench coat plant to make face masks and nonsurgical gowns. It was more than a feat of factory retooling. Flexible supply chains played a critical role, including rapid raw material sourcing, product design, development and testing, and distribution.
Getting started
Leaders invest in five capabilities to create resilient supply chains:
Network agility. Reacting quickly to disruption requires a flexible ecosystem of suppliers and partners that can handle sudden shortfalls or even produce new products. That means setting up alternative manufacturing sites and assembly nodes and making the most of Industry 4.0 tools to optimize cost, improve visibility across the network and accelerate reaction times. Leaders develop tailored solutions for each segment of their supply chains to boost performance and cut costs. Those dependent on offshore production move some manufacturing onshore or closer to their core markets. Toyota reduces risk by having one supplier produce 60% of the needed parts, and two additional suppliers each produce 20%.
Digital collaboration. Cloud-based supply chain applications and collaborative platforms and tools enhance information sharing. They also improve the quality and speed of decision making within an organization and with suppliers and other external partners in a secure environment. Amid the Covid-19 pandemic, manufacturers have demanded greater visibility into the supply chains of their suppliers—a practice worth continuing. Leaders are applying automation and robotics to make their supply chain more autonomous and adding suppliers in their home markets to ensure business continuity.
Real-time network visibility. Control tower solutions that integrate data across the entire supply chain, 5G technology and blockchain offer leadership teams real-time visibility. Companies can better calibrate supply with forecast demand by comparing internal production capacity data with real-time demand signals such as weather data.
Rapid generation of insights. Leadership teams can stay a step ahead of supply chain disruptions by improving their ability to rapidly analyze internal data and external sources of big data. That means harnessing machine learning and artificial intelligence for predictive and prescriptive analytics. Those tools can deploy early-warning technologies, model risk scenarios and develop preprogrammed responses. Increased risk of disruption also requires updated planning parameters and objectives, since old assumptions are no longer valid.
Empowered teams. Decentralized teams can react quickly to insights generated by advanced analytics and create the rapid-recovery capabilities that will help companies navigate smoothly in times of disruption.
The frequency and intensity of shocks to the global economy are increasing. The Covid-19 outbreak has exposed just how vulnerable far-flung supply chains have become. What long passed for adequate flexibility is now subpar. Companies that begin investing today in a resilient supply chain will be best positioned to weather the next event that obstructs the global flow of goods.
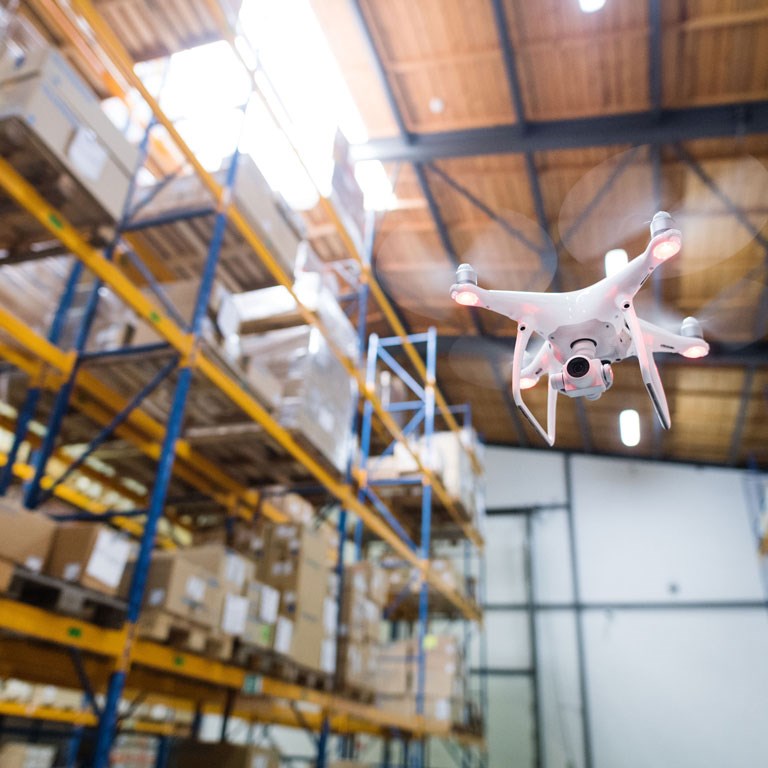
Operations Excellence
Companies with best-in-class operations have a strong competitive edge. Bain's insights on operational excellence help leadership teams transform supply chains, procurement strategy, and manufacturing capabilities into strategic weapons.

Coronavirus
The global Covid-19 pandemic has extracted a terrible human toll and spurred sweeping changes in the world economy. Across industries, executives have begun reassessing their strategies and repositioning their companies to thrive now and in the world beyond coronavirus.
Olaf Schatteman, Drew Woodhouse and Joe Terino are partners with Bain & Company’s Performance Improvement practice. Olaf and Drew are based in Bain’s Sydney office, and Joe is based in the Boston office.