Etude

En Bref
- While large automakers and Tier 1 suppliers have made progress decreasing emissions from their operations and energy use, upstream supply chain emissions remain a challenge.
- Supply chain decarbonization will become increasingly critical as passenger electric vehicle sales are forecast to rise to more than 75% of new vehicles sales by 2040.
- Electric vehicles have more than double the upstream emissions as combustion engines because of the embedded carbon content in batteries.
Decarbonization has become a front-and-center issue to nearly everyone: customers, business leaders, regulators, and investors—to name a few. But not all aspects of decarbonization have been addressed equally, especially in certain industries amid transformation such as the automotive sector.
While large automakers and the companies that supply them with key components have made progress decreasing Scope 1 and Scope 2 emissions by 8% and 9%, respectively, since 2017, Scope 3 emissions remain a challenge across the industry. Scope 3 emissions include the greenhouse gases emitted throughout the supply chain (upstream) and those emissions generated consuming a product (downstream). These are in contrast to a company’s direct emissions (Scope 1) and indirect emissions generated by purchased energy (Scope 2).
Even leading automotive original equipment manufacturers (OEMs) have only reduced their upstream Scope 3 emissions by 2% since 2017, while Tier 1 suppliers have actually increased their Scope 3 emissions (upstream) by 5% during the same time frame, according to recent Bain research. This data includes the average of leading companies that chose to report (it is not required), which means that the broader industry’s Scope 3 emissions are likely even greater (see Figure 1).
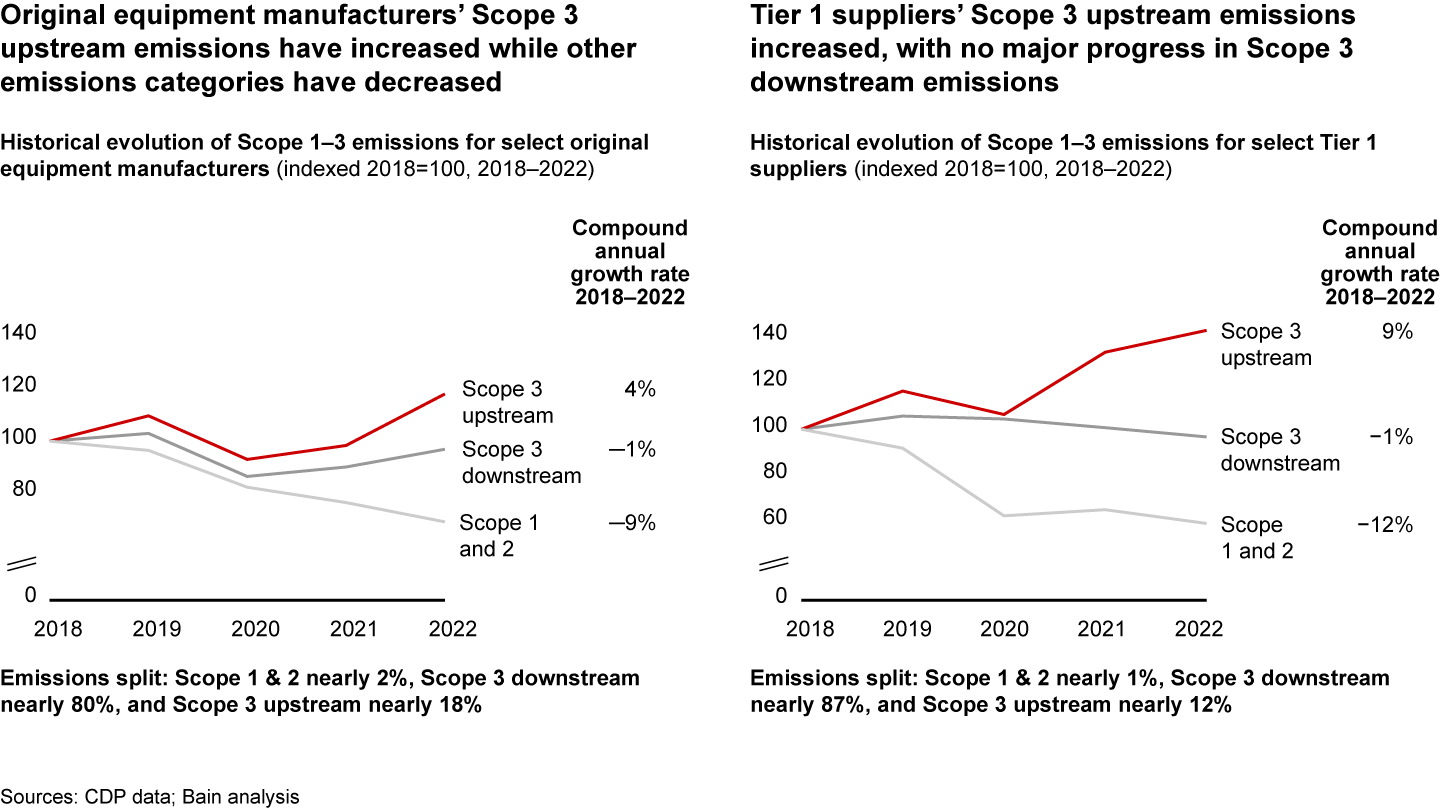
Winning companies that are making progress decarbonizing their supply chains succeed in four key areas:
- They set ambitious but achievable targets.
- They identify tangible decarbonization levers across the full value chain.
- They build a sequenced decarbonization roadmap, balancing trade-offs.
- They move quickly from strategy to action.
Supply chain decarbonization is certainly not easy, but it can create significant commercial and enterprise value. And being a frontrunner comes with considerable benefits to both OEMs and suppliers.
The decarbonization challenge and opportunity
Why have upstream Scope 3 emissions, in particular, remained a challenge in the automotive sector even as other types of emissions, including downstream Scope 3 emissions, are addressed? There are several reasons. First, supply chain decarbonization requires a transparent baseline. This is particularly challenging in the auto industry given the huge number of suppliers in multiple tiers. In addition, emissions are difficult and costly to abate, and to do so, various players across the value chain, from raw materials suppliers to OEMs, need to collaborate. Finally, many of the metals that are needed to build car components, from the chassis to the engine to the gearbox, are energy intensive to produce.
Automotive supply chain decarbonization is becoming more critical as electric vehicles (EVs) begin to take an increasingly greater share in the global fleet. Bain forecasts suggest battery EVs will rise to more than 75% of new vehicle sales by 2040. And since electric vehicles have a much higher proportion of upstream emissions than combustion vehicles, mainly because of the embedded carbon content in batteries, upstream Scope 3 emissions are becoming a greater focus. As a result of this, the circularity of EV batteries is also becoming even more important.
As many OEMs make commitments to carbon neutrality and as decarbonization is part of the criterion in their procurement and awarding processes, it has essentially become a must for suppliers of carbon-intensive materials and components. Suppliers who do not fulfill OEM requirements will be penalized or excluded from new businesses. OEMs also need ambitious net-zero targets both to secure investors and to be competitive with the large number of new challengers in the market.
Moving early is key. By decarbonizing the supply chain ahead of competitors, the market will be less crowded, and it will be easier to sell lower-carbon products to customers and gain market share. In addition, investors tend to give higher valuations to companies with a lower carbon footprint. Finally, by starting before others, it will also be easier to secure access to raw materials that can be limited, such as recycled aluminum or green steel.
The roadmap to supply chain decarbonization
Establish a baseline. Perfect is the enemy of good when it comes to baselines. Winning firms get started by establishing a greenhouse gas emissions baseline based on weight or expenses and then enhance the baseline over time by incorporating value chain assessments and adding real-time supplier emission data to enable continuous monitoring of progress.
For OEMs, key emissions sources are often battery cells, steel, aluminum, resins, and logistics; selected Tier 1 suppliers’ emissions are driven by the same metals plus textiles, electronic components, synthetic and natural rubbers, and other metals, including copper and magnesium.
Set targets. Successful automotive companies start decarbonizing the supply chain by setting targets that meet customer and investor expectations. First movers also consider the Science Based Targets initiative (SBTi). Many automotive companies do not yet meet the minimum SBTi requirements that call for 2.5% absolute annual emissions reductions for Scope 3 targets over a period of 5 to 10 years, which implies a reduction of 25% from 2022 to 2032. Some OEMs and Tier 1 suppliers are only targeting 10% to 25% absolute reductions by 2030 to 2035 (see Figure 2).
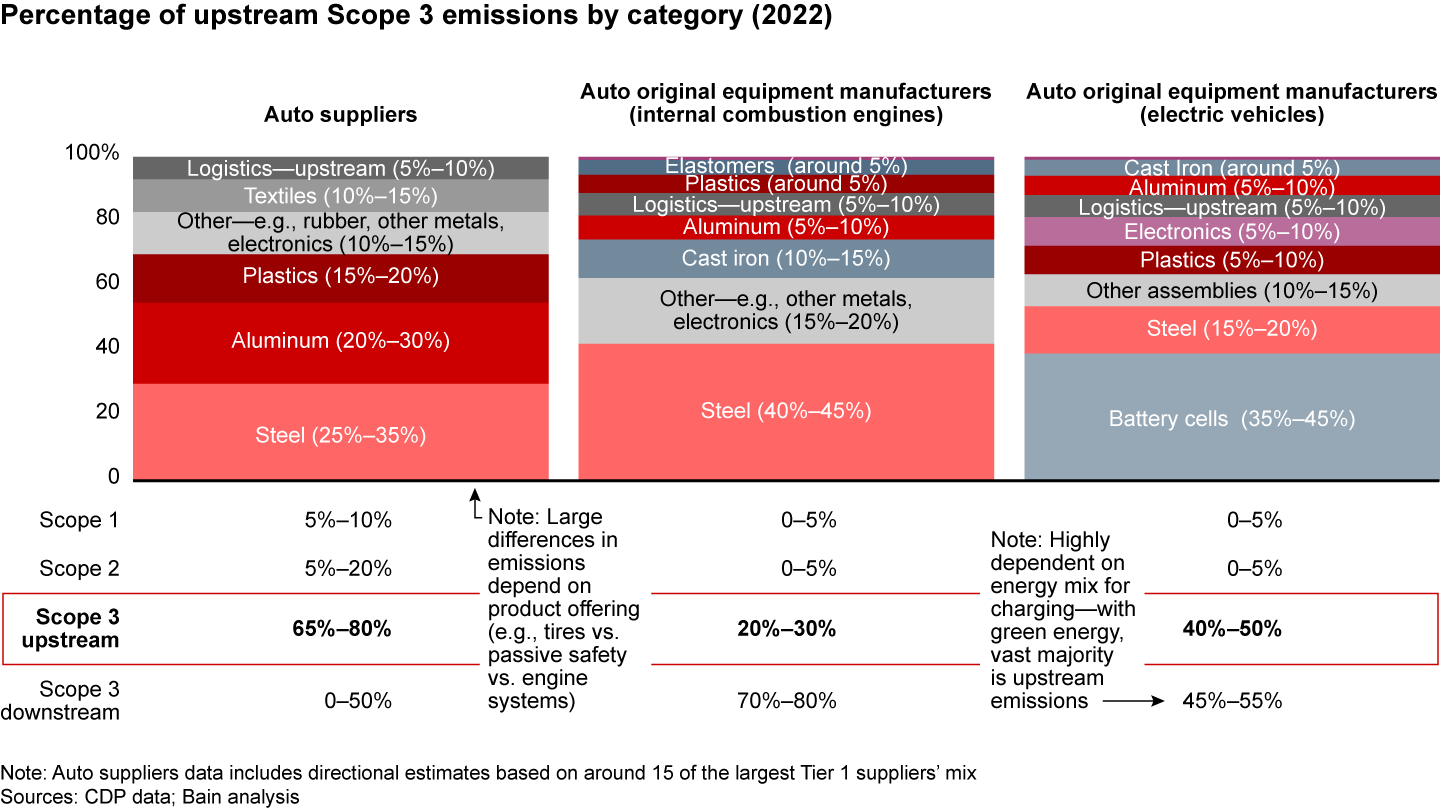
Identify and prioritize levers. With a baseline established, leaders identify and prioritize decarbonization levers. Levers can be organized in four key types: supplier management, volume allocation, product design, and value chain engagement (see Figure 3).
For automotive companies, often more than 40% of the decarbonization levers pertain to product design, and consequently, planning far in advance is critical as there is a long lead time to implementation. These design-related levers typically use greener or lighter materials and require cross-functional changes and value chain collaboration.
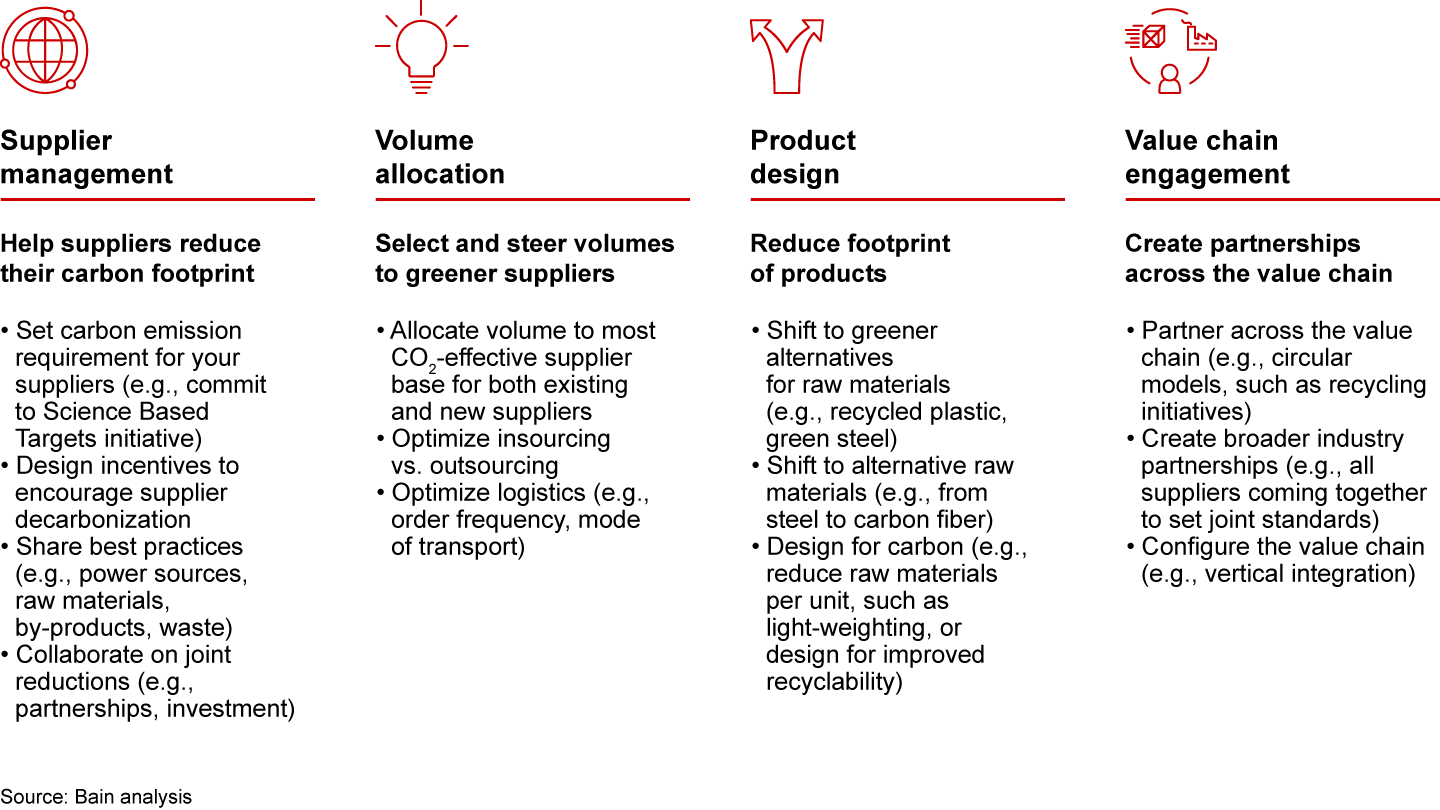
Make the right trade-offs. Identifying and prioritizing levers is the first step, but winning firms emerge by demonstrating their ability to sequence and phase levers correctly, ensuring their commercial viability and market maturity. For example, it wouldn’t make sense for a company to start by tackling electric truck systems or green air freight as these are not yet readily available on the market. At the same time, it may be possible to implement recycled materials faster and without a major cost impact, for instance, or it may be worth considering green fuel shipping, which is starting to become available as shipping players begin to help reduce emissions by offering methanol-based shipping.
In any case, leaders start by establishing which of the many levers will have a cost impact and any other trade-offs, such as the availability of technology, customer preferences, and technical features. Those levers that are cost neutral can be deployed in a cost-effective manner more quickly. For other, more expensive options, teams might mitigate cost through using less and lighter-weight materials or perhaps replacing magnesium with aluminum.
One major auto supplier, for example, started by identifying which levers had market maturity. It identified all the levers that could be implemented by 2030 that were cost neutral or better and with minimal capex and prioritized those while planning ahead for and securing longer-term levers for 2030 to 2040, such as greener materials and large redesign efforts.
Suppliers also need to evaluate when in the development phase they need to implement a given change. If they wanted to use recycled aluminum, for instance, when would it become available, and when would they need to substitute it? Will a given decarbonization measure be available within the next three years, and if so, could it go into the next vehicle generation? Or if a decarbonization measure might take longer, it could be better to consider it for the next platform (platform development cycles typically take around 15 years).
With all of this information, the supplier created a diligently phased roadmap based on cost, availability of the tech or solution, where in the cycle it must be implemented, and the customer’s willingness to pay for it. Using this information, it sets the sequence of actions.
Embed supply chain decarbonization in the operating model. Leading firms redesign their operations to establish cross-functional links and ensure that key processes, supplier engagement, and technology all support decarbonizing the supply chain.
The best teams embed decarbonization in all key processes (e.g., strategic planning, new product development) so that they can make the right trade-offs among carbon footprint, cost, performance, and customer experience. Setting an internal carbon price, for instance, can help leaders evaluate the trade-offs of carbon vs. cost or to evaluate which Tier 1 supplier will receive a given reward.
In another example of embedding supply chain decarbonization, a leading OEM is not only setting minimum carbon requirements for the short term and longer term but it is also specifying the materials required to be considered for rewards. These requirements could include, for example, 90% recycled aluminum, green steel, or that the energy used when producing plastic parts has to be 95% green. Similarly, automotive OEMs and suppliers have started to introduce carbon and the cost of carbon as part of the equation when evaluating suppliers for awards. Premium automakers are putting part of the weight of the reward on the supplier’s carbon maturity.
Forward-looking firms segment suppliers based on emissions, criticality, and carbon maturity. They focus on the strategic suppliers with the highest carbon reduction potential first, then they align with customers and collaborate along the entire value chain in order to decarbonize the product. Firms also help enable suppliers to make investments into decarbonizations through measures such as awarding long-term business to those suppliers or coinvesting with them.
Finally, leaders use data and carbon accounting tools to track in real time how decarbonization levers are being implemented and whether actual carbon levels are being reduced as well as for establishing a single source of truth.
Six questions leading automotive executives are asking today
To understand how close their company is to making decarbonization a source of competitive advantage and a core operational capability, winning executives are asking the following six questions:
- Do our supply chain decarbonization targets reflect stakeholder requirements and value creation potential?
- Do we have a reliable carbon baseline that enables fact-based decision making?
- What are our short- and long-term priorities, and have we optimized our decarbonization roadmap against those priorities?
- Do we have a cross-functional approach that includes perspectives from procurement, marketing, strategy, R&D, and sales?
- Have we factored decarbonization investments into our business planning?
- Do our standard operating procedures (such as tenders and rewards) and our product design guidelines include carbon considerations?