Technology Report
Executive Summary
- The semiconductor shortage won’t end on a single date. Some companies are starting to see relief this year, while others may have to wait until 2024 or later.
- Softening demand is the fastest route to relief, and it’s conceivable given the slowdown in the global economy.
- Leading companies are designing their products to increase resilience, systematically assessing risks, investing in value chain innovations, and revamping their operating model.
This article is part of Bain's 2022 Technology Report.
As the global semiconductor shortage drags on, every tech executive is asking the same question: When will it end? But the more salient question might be: When will my company get relief?
The reality is the chip crunch probably won’t end on a single date. Many disruptive factors continue to dog semiconductor supply chains—acute events such as Covid-19 lockdowns and extreme weather that lead to short-term operational disruptions, as well as structural supply chain weaknesses that have caused shortages of “leading-edge” 12-inch wafers with transistors of 28 to 130 nanometers, “lagging-edge” 6- and 8-inch wafers, and advanced substrates for “bleeding-edge” chips with transistors of 5 to 14 nanometers. Each has its own timeline to resolution. As a result, some companies are starting to see relief this year, while others may have to wait until 2024 or later (see Figure 1). At the same time, several wild cards could cause more disruption, including the global economy, geopolitical tensions, and shortages of equipment for manufacturing bleeding-edge chips.
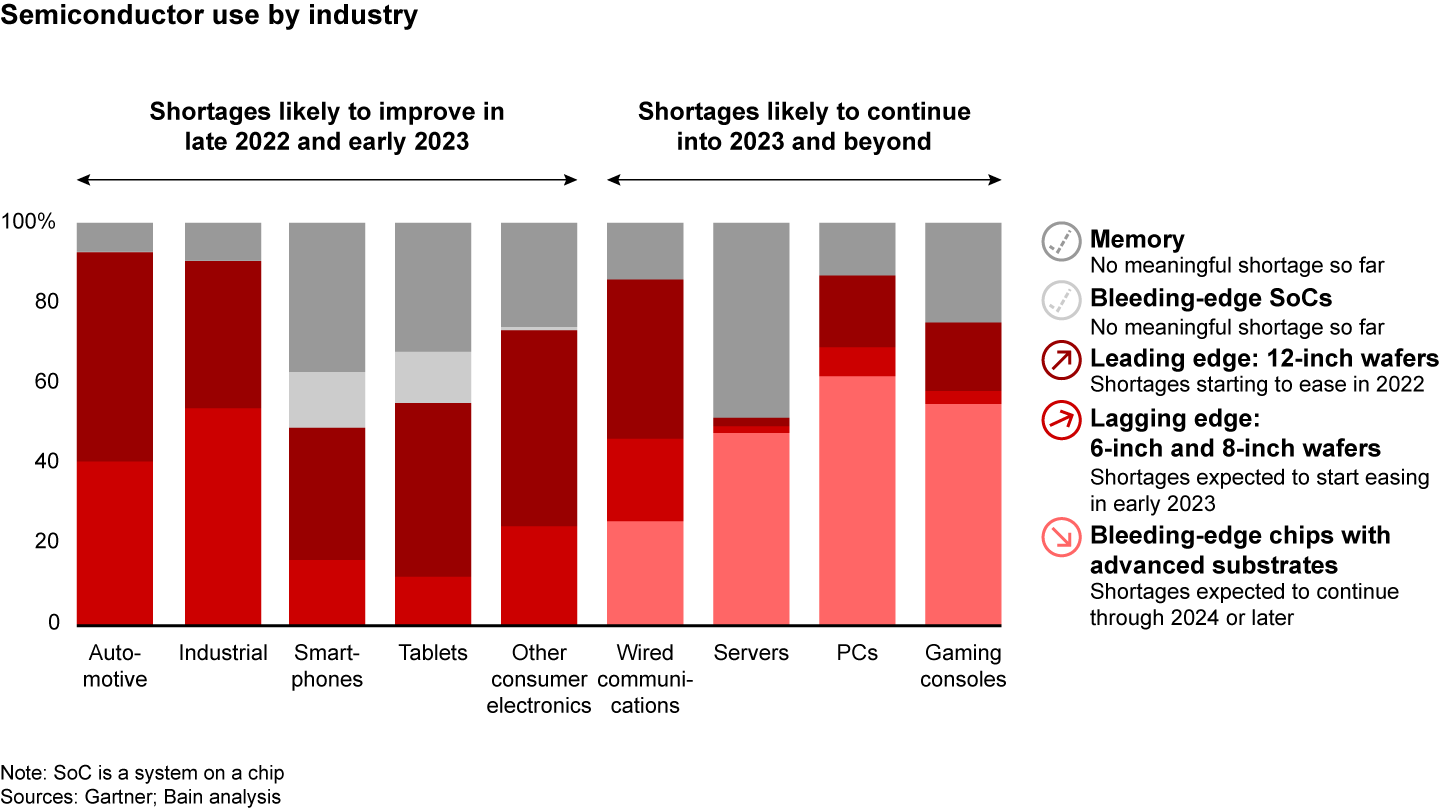

Many have followed how automotive companies cut back orders when Covid-19 hit, only to find themselves at the back of the line for wafers when they later needed them. But the larger impact has come from skyrocketing demand for technology products, and the long lead times required to build the fabrication plants that supply their chips has led to a chip shortage that has often played out unevenly but has affected nearly every end market in some way.
Some chip types (and the industries that rely on them) have been hit harder and at different times. After shooting up in 2021, lead times for chip deliveries have flattened at elevated levels in recent months (see Figure 2).
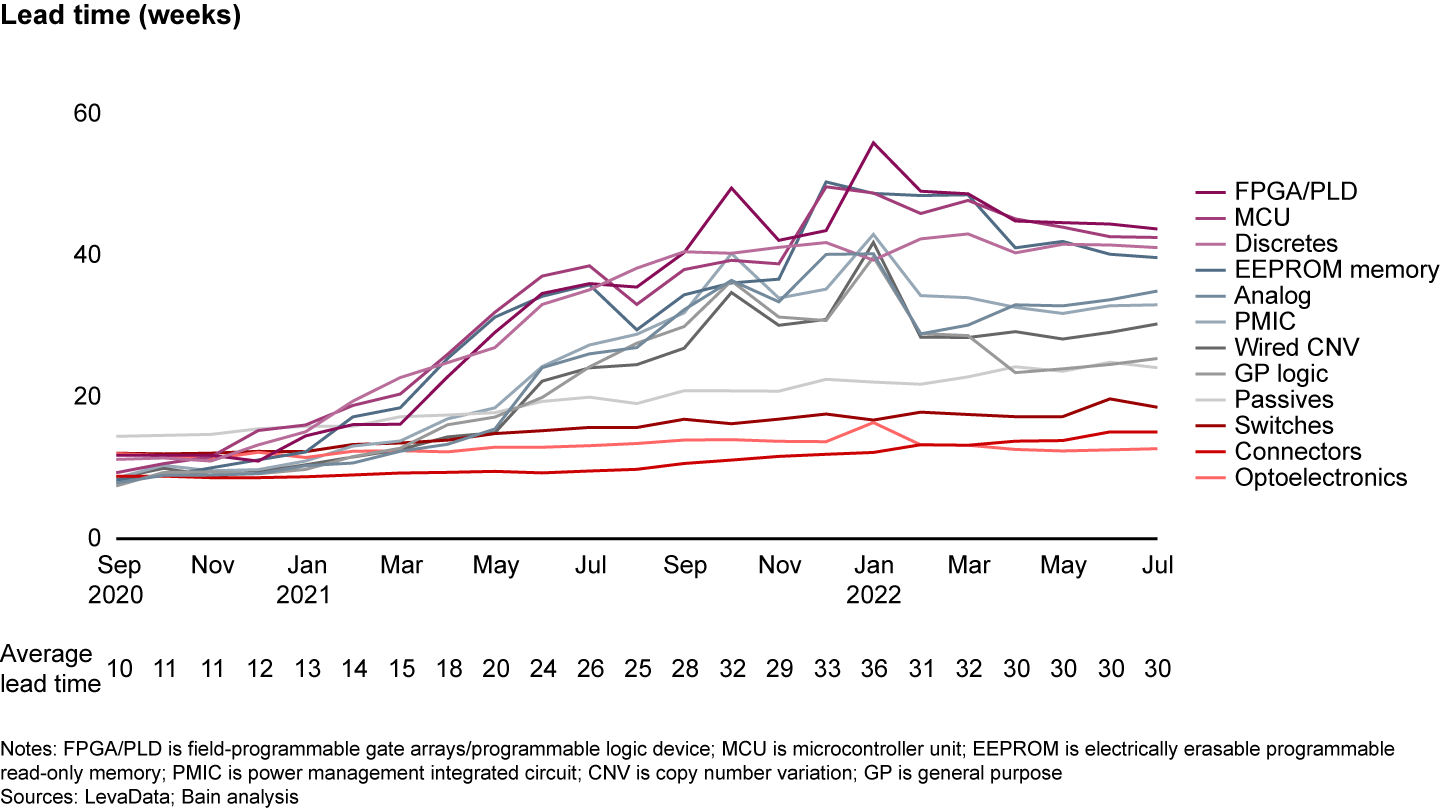

These shortages will improve faster for certain products and industries, depending on the types of chips they use, but more tech executives are recognizing that the next phase of the shortage will be like the arcade game Whac-A-Mole. As one shortage recedes, giving affected chip buyers all the computing components needed to produce a complete product, those buyers will start to consume chip supplies in another area, causing new shortages to pop up.
Three wild cards will determine how the shortage plays out.
- Demand pullback. Unfortunately, the fastest route to relief is softening demand. Inconceivable for the past 2 ½ years, this now seems a distinct possibility, given the economic outlook. There are already reports of tech companies temporarily pausing new component orders and asking suppliers to delay or shrink shipments amid inflation worries and growing inventories.
- Shortages of extreme ultraviolet (EUV) lithography equipment. These $150-million-a-pop machines are necessary to build bleeding-edge fabrication plants, and there’s only one supplier, ASML. This bottleneck will likely grow over the next three years or so, potentially constraining capacity and limiting new plant openings at a time when semiconductor makers plan to spend well over $150 billion on new bleeding-edge production facilities (see Figure 3).
- Geopolitical frictions. The semiconductor supply chain has become a major strategic asset in geopolitical maneuverings, and not just in China and the West. This year, Russia limited exports of noble gases, including neon, a crucial ingredient in chipmaking. That followed Japan’s 2019 restriction of exports to South Korea of high-purity hydrogen fluoride, an etching gas used in semiconductor manufacturing. Growing tensions between China and the US threaten to further bifurcate the global technology ecosystems. The US has already cut off China from receiving advanced tools, and domestic-first policies in China may make it difficult for Western firms to access lagging-edge chips from China, where there’s a concentration of lagging-edge wafer manufacturing hubs coming online. And these are just a few of the reasons that semiconductor consumers will need to increasingly consider geopolitical risks when sourcing their chips.
These wild cards are largely out of tech executives’ control, but companies can take several pragmatic steps to protect themselves against chip shortages and the myriad disruptions to electronics supply chains that are undoubtedly coming.
Design products for flexible resilience. Leading companies constantly refine their products to increase resilience, ideally beginning early in product development and before a supply disruption hits. In our work with clients and analysis of the global landscape, we’ve found that certain things consistently succeed: reducing a product’s number of parts, reusing components, using standard design approaches and flexible product architecture wherever possible, and decoupling software from hardware. In a chip shortage, for example, the fewer “hooks” the product has into silicon, the better.
Assess risks regularly. To help identify the next big supply crunch, leading companies proactively and continuously assess risks across their entire supply chain and all scenarios they can imagine. After chasing parts for 18 months, one global technology company recently stepped back to evaluate the potential magnitude and duration of a wide range of risks, including those related to specific suppliers, natural disasters, and geopolitical tensions. This helped highlight where investment was most critical to shoring up supply chain resilience. To reduce its reliance on a single supplier for key components, the company had to pay extra to keep multiple suppliers active and bring its procurement department into product development discussions earlier. As a result, the company should be able to fulfill more orders during the next major component shortage, potentially saving several hundred million dollars of revenue it would have otherwise lost.
Get closer to the semiconductor supply chain. In this era of increasingly frequent and intense supply disruptions, traditional supply chain approaches won’t cut it. Many leading tech companies are developing closer relationships with their suppliers and the semiconductor ecosystem. Some are subsidizing suppliers’ production capacity in exchange for a guaranteed, agreed-upon volume of product. Foxconn has gotten even more hands-on, forming joint ventures to build chip fabs in India and Malaysia. Others are doing more semiconductor design in-house and developing new capabilities to do so.
Revamp the operating model. To pull all of this off, leading companies are refreshing their operating model to improve collaboration among engineering, sales and marketing, and procurement—the teams critical to managing through and preparing for supply disruptions. For example, these companies create rapid feedback mechanisms to help the three departments communicate better and prioritize the most important customer requests and the highest-value product redesign opportunities. They further strengthen these operational muscles by emphasizing cross-functional collaboration in their training programs.
After two years of chaos, some tech companies are finally starting to see some relief from the chip shortage. The recovery will be choppy, but leading companies are moving quickly to control what they can, investing in supply chain resilience so they’re ready for whatever comes next.