Brief
Around the world, manufacturers have spent the past 50 years implementing a range of programs and techniques to reduce costs and improve product quality and customer service. Lean, total productive maintenance (TPM), total quality management (TQM), Six Sigma and, in some cases, full production systems have yielded solid results. We’ve seen companies that leverage these approaches well—such as Toyota, Procter & Gamble, and Danaher—boost productivity by 6% or more a year.
Those investments aren’t obsolete, but they also aren’t enough. To compete effectively in the future, you need to rethink what’s possible today.
Two critical developments have raised the bar for manufacturers as they pursue a factory of the future strategy. On the opportunity side, game-changing digital and Industry 4.0 technologies have redefined what’s possible for next-generation production systems. When properly deployed, these new capabilities can raise productivity by more than 10% and create a host of additional advantages regarding flexibility, quality, consumption of natural resources, capex allocation, labor savings, and more.
To cite just a few digital possibilities, artificial intelligence (AI) could, in essence, read a customer’s mind, predict demand, and steer products along individual paths through the supply chain (not to mention generate artwork, as with the image above), while production units become self-healing and self-learning, freeing humans to focus on creative tasks and supervision. The many benefits of digital aren’t lost on leading companies. In a recent survey of 270 manufacturing executives around the world, respondents who say digital is well-integrated into their production systems are three times as likely to say they’re close to achieving their production system goals, compared with those who lack high levels of integration.
But those opportunities to achieve value at scale are matched—and made more compelling—by a growing list of challenges affecting the manufacturing sector. Chief among them is the sustainability imperative, as customers, employees, regulatory bodies, and other stakeholders call for marked improvements across a wide range of decarbonization, circularity, and related metrics. Manufacturers also face new competitive pressures and increased customer expectations that require more flexibility and customization, shorter time-to-market cycles, higher-quality products, and other changes to how they operate.
That’s why it’s critical for manufacturers to pursue a more innovative supply and production system. This critical component of the factory of the future integrates the traditional approaches mentioned above with cutting-edge digital capabilities, enabling you to accelerate your sustainability efforts, optimize processes and workstreams, and transform how you bring products to market.
Many companies fail to get the most from new digital and Industry 4.0 technologies because they bolt them on as attachments, rather than integrating them into their existing manufacturing environments. Companies often take a “digital for the sake of digital” approach, focusing on single use cases rather than adopting an end-to-end perspective that connects digital to their lean, TPM, TQM, and Six Sigma investments.
A focus on sustainability
That nonintegrated approach has many drawbacks, and one of the biggest is the missed opportunity to effectively address sustainability. In the same survey cited above, we found that many respondents expect sustainability to become their top agenda item two years from now (see Figure 1), vaulting it into a near-tie with productivity.
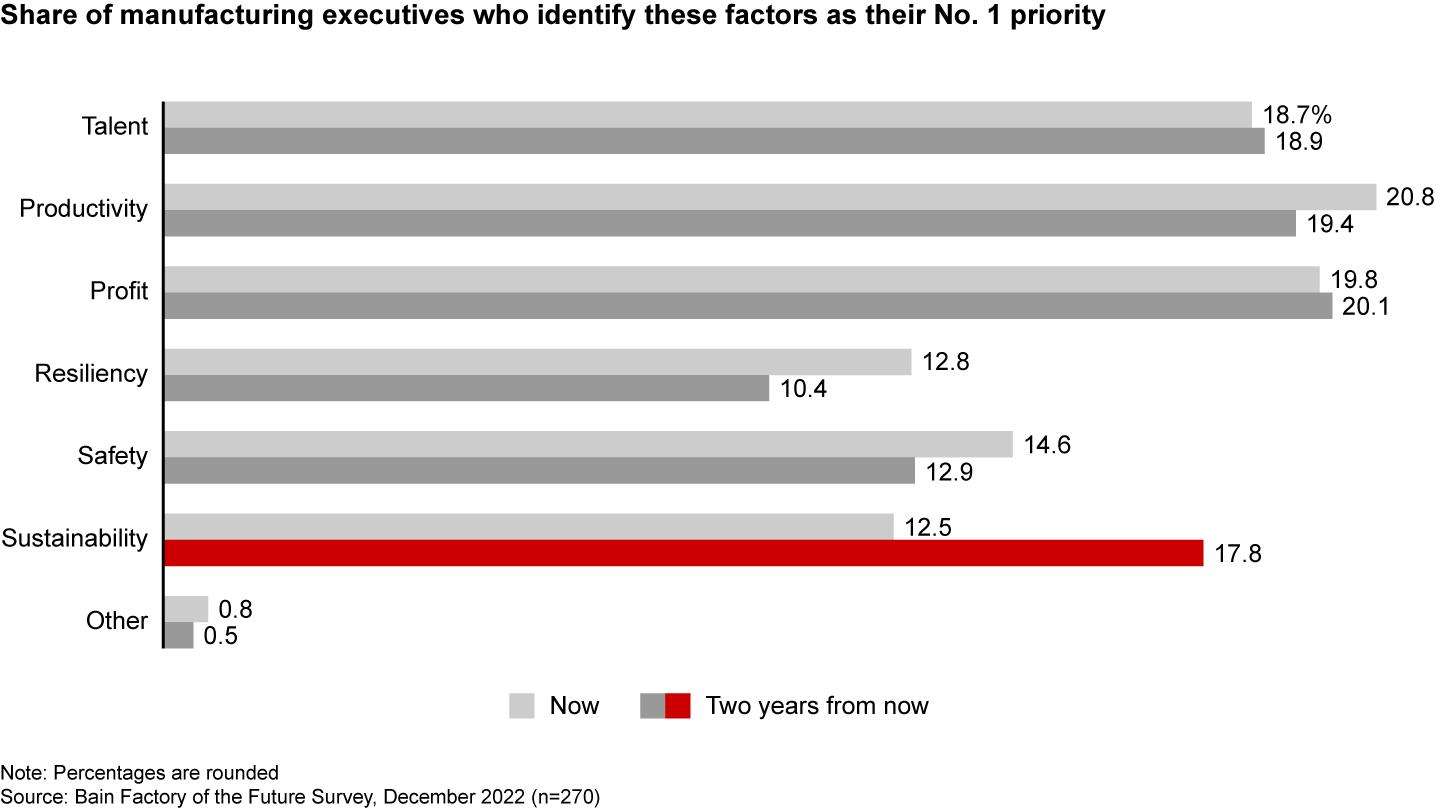
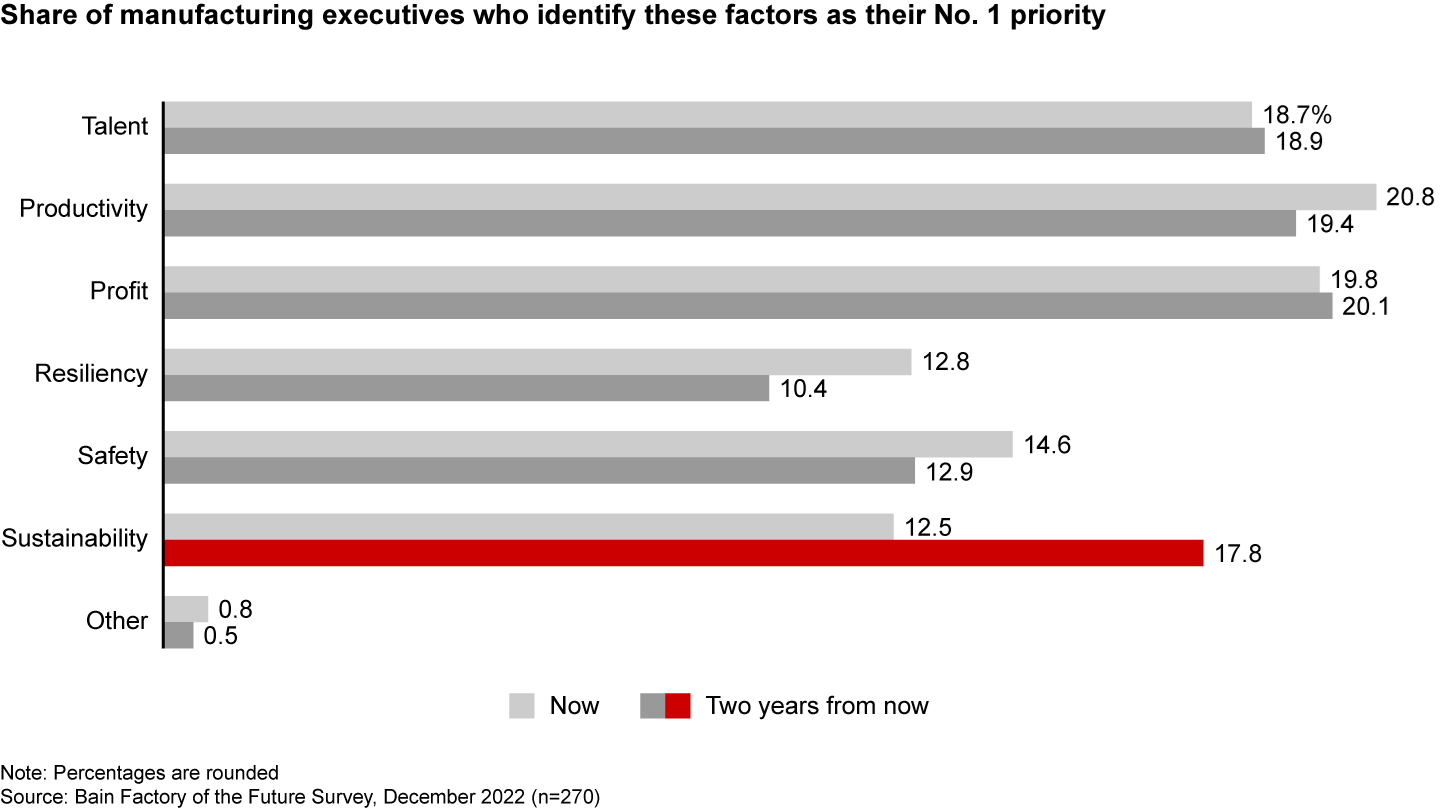
Sustainability issues are increasingly complex and profoundly impact a company’s end-to-end value chain, from design and sourcing through transport, use, and disposal. Carbon emissions, water scarcity, labor practices, government regulations, and rapidly evolving consumer expectations are just some of the factors pushing sustainability high up the priority list.
Many of these challenges are interconnected and can be adequately addressed only by a production system that’s well-integrated and powered by digital technologies across the entire value stream. Our approach recognizes that sustainability and circularity should be regarded as an essential pillar in a fully integrated supply and production system, rather than being addressed as separate, ad hoc efforts.
An integrated system based on a clear digital strategy is key to translating your company’s stated goals for sustainability into the shop-floor actions and decisions that turn that ambition into reality. It supports increased circularity to help you create a positive impact on the environment.
Rethinking what’s possible
A fundamentally new approach to your production system—one that combines strategic principles with the methods and tools that bring those principles to life—will solve those issues and catapult you into a leadership position. Our integrated system applies a framework of design principles and specific elements that begin at the individual workstation and extend across the organization and beyond, to the entire value chain. A careful analysis of your maturity level(s) guides the prioritization and deployment of these principles and elements, ensuring that you have a solution tailored to your current and future capabilities and ultimate ambition (see Figure 2).
To make those principles tangible, we link them to dozens of discrete elements that span your operations, from workstations to production lines, ultimately extending beyond the walls of your organization.
These elements fall into two broad categories: your network and supply system, and your factory production system. The former includes elements such as supply chain connect, design for operations, manufacturing footprint, circular design (a key element as companies bring their sustainability strategies to life by integrating sustainability and circularity principles with these core systems), and more, each made up of several components that can be deployed in sync with a given need or ambition.
The latter includes modules such as smart quality management, connected lines, synchronized four walls, next-generation IT and data foundations, safety-oriented culture, self-learning organization, and many others, each composed of several specific capabilities and attributes.
For example, smart production processes would include elements that address manufacturing (such as muda/waste reduction, standardized work instructions, and flexible workstations), smart quality management, and reliable asset health. Sustainability and circularity would include elements such as circular value streams and circular design, sustainable four walls, and a safety-oriented culture. Synchronized value streams would encompass supply chain capabilities such as end-to-end traceability and flow planning, as well as strategic make vs. buy decisions, flexible plant layout, next-generation IT and data architecture, and many more.
In total, there are more than three dozen elements that can help transform your supply chain network and factory to a future-ready system, starting today.
Not every element will pertain equally to every company. The key to getting started is to determine which of the pillars and associated elements are most relevant to your industry and product mix, and tailor a factory of the future approach that’s right for you. For example, one-piece flow is an important focus for many discrete manufacturers, but not for capex-intensive continuous-process industries, where reliably centered maintenance would be a top priority.
A smart start also includes taking stock of what you’ve already implemented, so you can build on it. Most companies have embraced some standards based on TPM, lean, Six Sigma, or full production systems, providing a foundation that can be upgraded or redesigned by incorporating new digital technologies. Our survey finds that this integration is essential to value realization at scale. Companies that have effectively integrated digital into their production systems are significantly closer to reaching their production system goals than those that have not, by a better than 3-to-1 margin.
The future begins now
A future-oriented network, supply, and production system provides a clear path to autonomous manufacturing, ushering in an era of:
- Shop floors that are digitally enabled (for standard operating processes) and AI-supported (addressing reliability maintenance). For example, companies can make enormous progress toward an era of smart maintenance, in which AI-driven analysis of machine data can sense, decide, and act to optimize maintenance based on the impact to operations.
- Flexible plant layouts powered by line-less mobile assembly systems, stationary and mobile robots, autonomous mobile manipulators, vision-based localization algorithms, and other state-of-the art digital and wireless technologies.
- Robust, circular value chains that connect suppliers and customers, minimize waste, and enhance material management.
- Adaptive organizations that embrace AI-supported problem solving and other techniques to continually and automatically improve how they operate.
The journey to this future state will vary by company, by plant, and even by specific value stream within a plant, depending on the maturity level and the short- and long-term ambitions they’ve set for each. Ambition levels will depend, at least in part, on a careful cost-benefit analysis. Companies at a higher maturity level will need to consider the level and types of technologies required (from sensors to fully integrated digital solutions), the necessary IT infrastructure required to scale, and the skill sets to develop (or gaps to fill) to effectively operate a factory of the future.
Those costs and complexities will, of course, need to be weighed against the expected improvements in flexibility, cost, sustainability, product quality, customer responsiveness, and many other potential benefits. We can help you analyze these rapidly evolving possibilities and tailor an approach that meets your strategic needs and accelerates your progress to the factory of the future.