Brief
At a Glance
- Even as they reel from the tragedy of the Russia-Ukraine war, executive teams need to keep their supply chains functioning, just as they did during the Covid-19 pandemic.
- Our analysis of the likely short- and long-term impact of the invasion anticipates broad pressures on companies’ raw materials, logistics/transportation, teams, and infrastructure.
- Companies should assess and prioritize risks across the value chain, monitor changing risk signals, actively counter the persistent headwinds of inflation, upgrade risk mitigation strategies, enhance supplier base traceability, and refine their operating model to support risk management and recovery.
The effects of war on the citizens of Ukraine are immediate and horrific. As shocked companies around the world help in any way they can, they’re also trying to understand the likely secondary impact of the Russian invasion on their employees, customers, operations, and supply chain.
The last of these preoccupations has been a familiar one for executive teams over the past decade or so, as a succession of national, regional, and international events shook the world and strained supply chains. The earthquake and tsunami that struck Japan in 2011. The 2015 port disruptions in the US (labor disputes) and China (storage explosions). Escalating trade disputes between the US and China, and Japan and South Korea. The United Kingdom’s exit from the European Union. That’s a far-from-exhaustive list of the turbulence.
And then Covid-19 emerged. The pandemic revealed many lingering vulnerabilities in global supply chains, causing leading multinationals to rethink their supply chain strategy to minimize similar disruption in the future. Amid the current crisis, some executive teams might now be cushioned by continuous improvements to their supply chain resilience undertaken since 2020. Other companies might be regretting reverting to a wait-and-see approach when lockdowns ended.
But regardless of how much they learned during the pandemic and other pivotal episodes in recent history, few companies will think they have a clear idea of how the war in Ukraine—one of the most dangerous and unpredictable developments since the Second World War—will affect their supply chain and for how long. Nor do the questions stop at, “How do we keep serving our customers?” There’s also the cost of maintaining continuity and the impact on sustainability efforts.
Amid ongoing shocks such as these, we find it’s helpful for executive teams to analyze the immediate and longer-term impact on raw materials, logistics/transportation, teams, and infrastructure. Below is our early assessment of the challenges in these areas, as well as a handful of no-regret moves that should help companies strengthen supply chain resilience in almost all scenarios for the war in Ukraine, while also guarding against future turbulence from other sources.
Challenges over the next three to six months
As surging commodity prices have already shown, the war in Ukraine is constraining the short-term supply of natural resources and other raw materials vital to businesses around the world, amid fears of worse to come in the months ahead.
For oil and gas, the volatility reflects the unwinding of partnerships between western and Russian energy groups, such as BP choosing to divest its shareholding in Rosneft and Shell cutting its ties with Gazprom. The impact of supply issues will vary by country and be heavily influenced by actions against Russian oil and gas exports (whether government-mandated or self-imposed). Gas is a particular vulnerability, with almost 40% of the natural gas consumed in the European Union originating in Russia. Italy and Germany are particularly exposed to fluctuating gas prices and supply, when the proportion of gas coming from Russia is considered in combination with a country’s overall dependence on gas as an energy source (see Figure 1). Also expect pricing pressure on oil-derived products such as naphtha, used in resins and plastics.
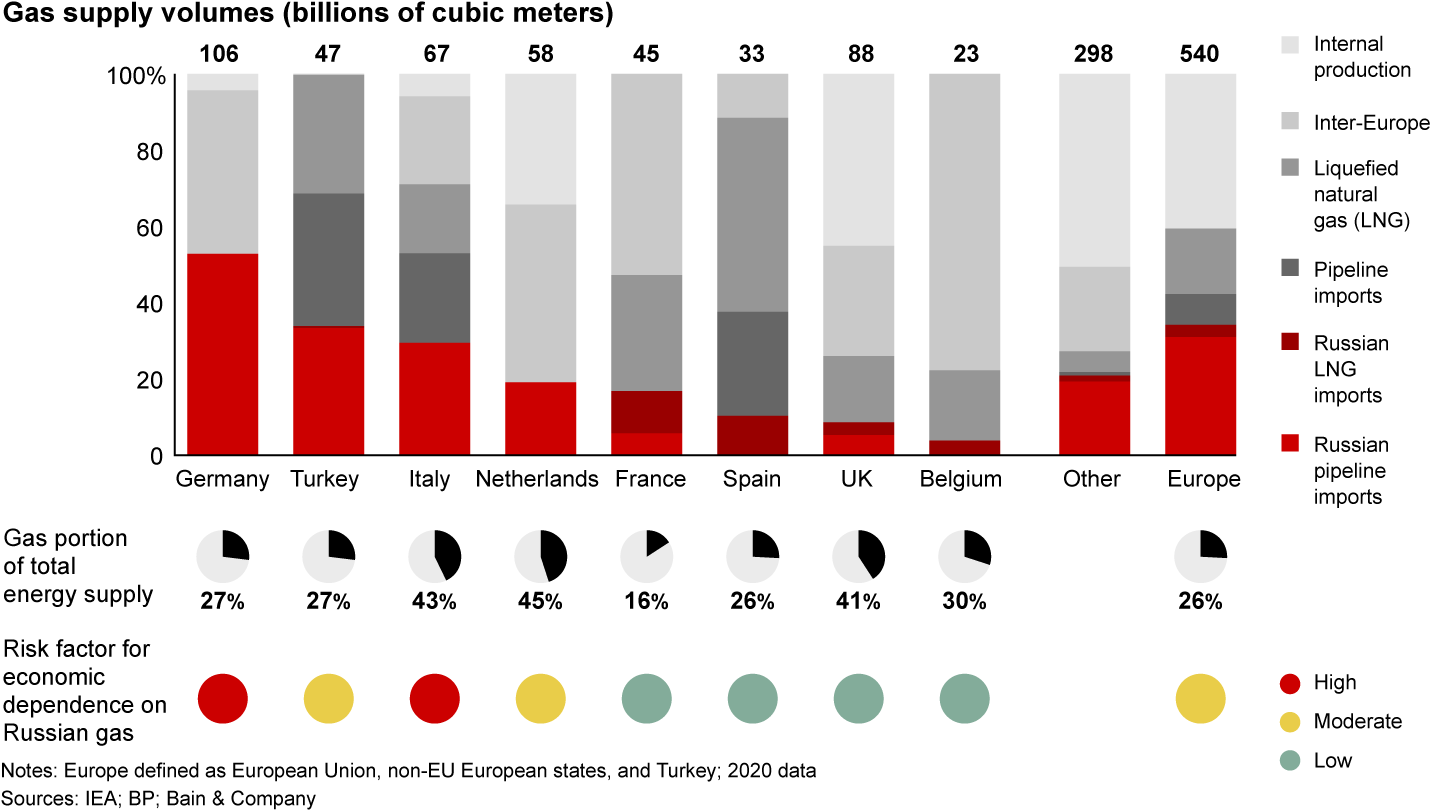
Agriculture is anxious about the short-term availability of commodities used in fertilizer, such as ammonia, potash, and urea. Their surging prices reflect the importance of Russia and Belarus as major global exporters of fertilizer and its components in peacetime. The impact has been felt as far away as Brazil, where farmers have been scrambling to secure fertilizer supplies. Wheat and corn prices may remain elevated given input cost trends and the importance of Ukrainian and Russian exports. Big grain importers such as Egypt, Turkey, and Nigeria could be disproportionately hit.
The price of steel and other commodities derived from natural resources (e.g., iron ore) may continue to rise, given Russia and Ukraine’s importance to supply. A very large chunk of the world’s supply of neon, vital to the production of semiconductors, is produced in Russia as a byproduct of steelmaking and then purified in Ukraine (see Figure 2). Germany’s automobile makers could be among those hit hard in the short term if semiconductor makers exhaust their inventories of neon and are unable to secure enough supplies to avoid a fresh chip shortage.
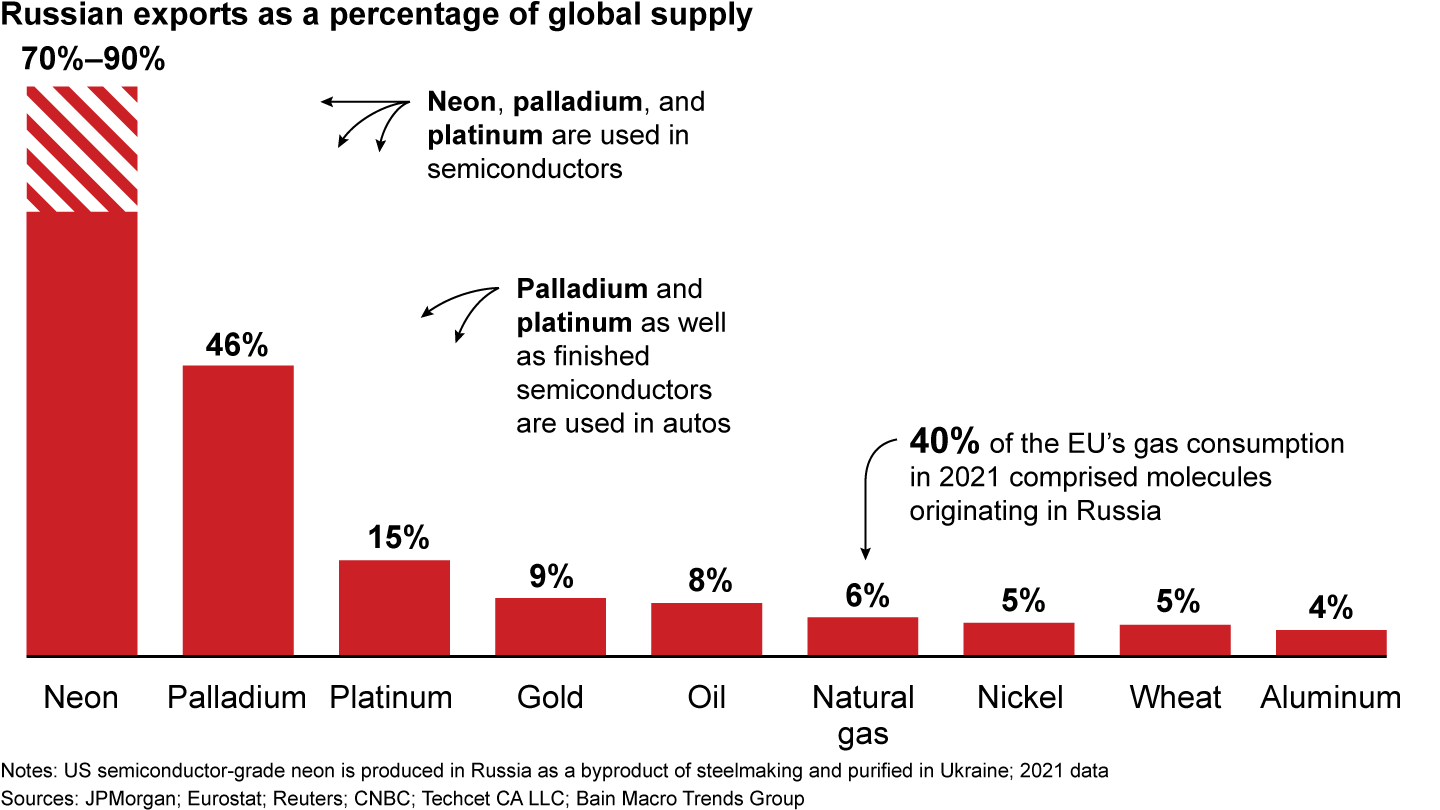
The humanitarian imperative to prioritize refugees is likely to have a knock-on impact on commercial air, road, and rail transport and logistics in western Europe, while war-related disruption to maritime traffic in the Black Sea is likely to continue. Companies still doing business and employing people in the region will face obvious short-term operating constraints given the conditions many of their workers are facing. Sanctions and independent decisions by companies may well further redraw local commercial boundaries. Worldwide, companies will have to cope with volatile demand in certain categories as consumers adjust spending amid soaring food and energy costs.
Longer-term challenges beyond six months
The outlook for raw materials (including energy) is mixed. Downstream agricultural products such as ethanol and other corn- or wheat-based derivatives are likely to be affected by production shortfalls and the diversion of supplies to food. Similarly, we expect trade restrictions with Russia to reduce the production and availability of key strategic metals, alloys, and other derivative metal products (e.g., batteries) that use materials such as nickel, tungsten, and neon gas.
However, steel prices may stabilize as international players increase steel production capacity (while trying to balance environmental commitments with any increased coal use needed to deliver that extra capacity). Until global capacity is rebalanced, the price of oil and gas may continue to rise further against a backdrop of deepening sanctions, especially as the winter heating season approaches.
Unless the conflict substantially escalates, road, rail, and air logistics should stabilize, although global disruptions may remain for air logistics, given Russian airspace restrictions and constraints on Ukraine’s heavy cargo capabilities. Similarly, most maritime routes should stabilize, although significant disruption may remain in and around Russia.
Companies operating in the region will likely have to reconfigure their labor pools in areas such as engineering and design, production, and logistics. Businesses worldwide may have to make their global supply chains more transparent to customers wanting to identify and manage future Russian exposure, as well as comply with trade restrictions. Similarly, their customers may also start to demand more flexibility and resilience in situations where global supply nodes are located in areas of heightened geopolitical risk. Catering to those demands for enhanced continuity planning could result in strategic redundancy and higher costs to serve customers.
On a macroeconomic level, the sanctions imposed on Russia could contribute to the end of the era of capital superabundance and capital globalization, constraining foreign direct-investment flows and influencing supply chain investment decisions. A marked increase in defense spending in the European Union and beyond could reduce government spending in other areas. Robust cybersecurity will be essential across the end-to-end value chain—from design through fulfillment. Global and company environmental, social, and corporate governance (ESG) agendas and commitments may also need to be recalibrated as geopolitical and trade bloc dynamics create inefficiencies and a potential delay in energy transition, resulting in prolonged reliance on coal-based energy.
Boosting supply chain resilience amid uncertainty
No company can afford to underestimate the significance of the war in Ukraine, even if it doesn’t seem to directly affect them now. It’s unclear how the crisis will resolve, or whether it sets a precedent that other geopolitical actors will follow. And in the wider analysis, the frequency and magnitude of supposedly once-in-a-generation shocks was already calling for an ongoing strategic response to improve supply chain resilience (see Figure 3).
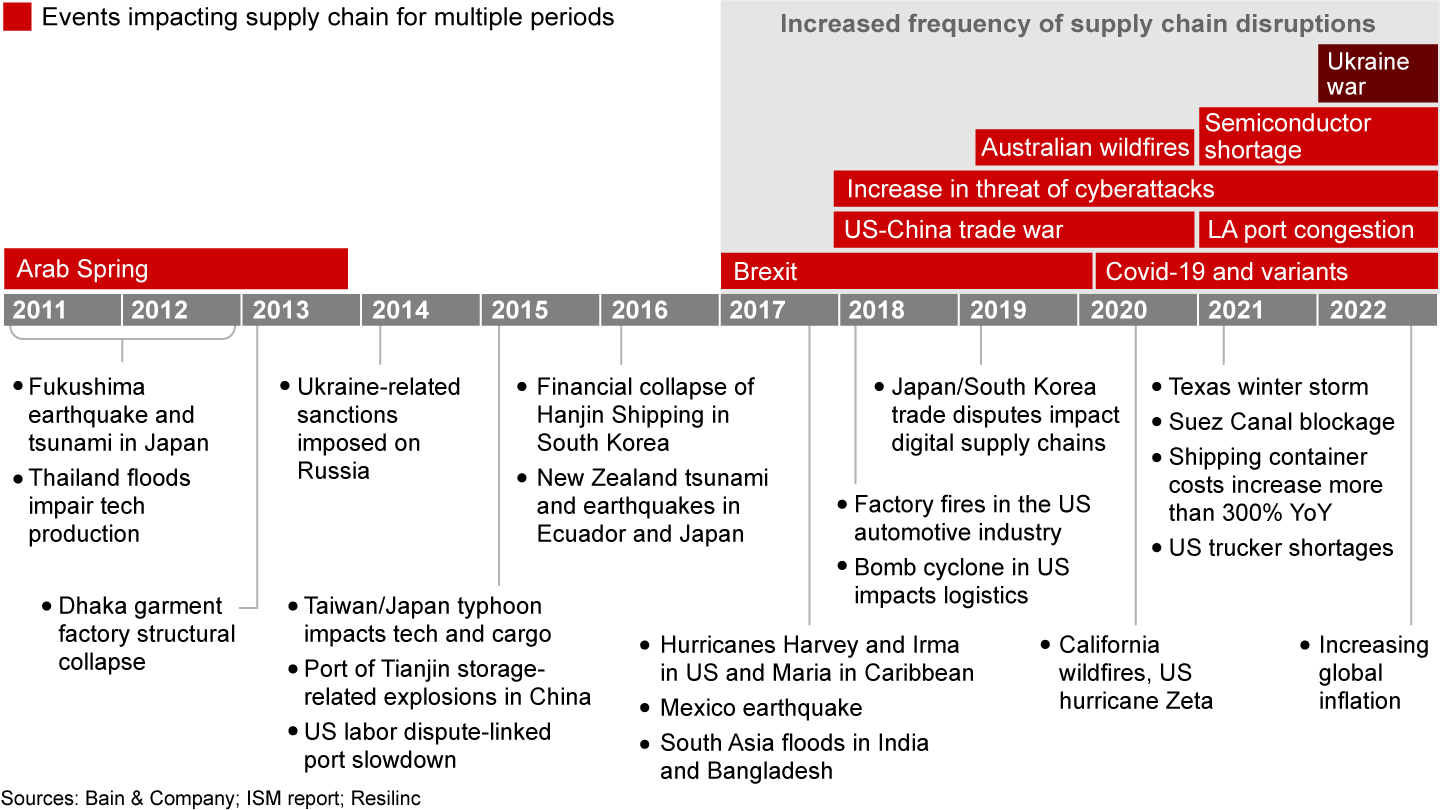
In addition to their urgent responsibility to safeguard staff and customers in the region, executive teams should consider a handful of no-regret supply chain actions, both to protect their business in the short term and transform their resilience over the next decade.
- Assess risks across the value chain, prioritizing key themes and single points of failure. Conduct a data-driven risk assessment of the value chain from product development and the supply base through production and fulfillment. For the key threats, evaluate probable scenarios and assess the potential magnitude of business and customer impacts across multiple dimensions (timeline, service levels, etc.)
- Establish signposts that predict changes to your supply chain risk profile and develop the capabilities to monitor them closely. Identify the key signals and leading indicators to flag potential risks such as geopolitical trade tensions, industry capacity-to-demand ratios, supplier health, and commodity capacity/geographic concentration. Develop capabilities to provide early warning notifications and establish processes to run simulations to inform and prioritize risk mitigation. Create a digital roadmap that embraces advanced analytics and leading technology for greater precision and accuracy.
- Actively counter the persistent headwinds of inflation. Cost management will remain a strategic issue across industries, as companies confront challenges related to volatile customer demand, commodity costs, supply chain constraints, and labor availability. Establish a cost management program that’s more than a match for inflation, offering visibility into cost pools, key performance indicators, and performance trends.
- Upgrade mitigation strategies for the most acute risks, while filling any gaps in your mitigation planning. Create a full set of mitigation options (e.g., product/process redesign, alternative sources, network structure, capacity buffers, back-up or flexible routes for logistics flows, etc.) informed by industry benchmarks and best practices. Specifically, for the supply base, clearly understand where you need to have surety of supply. For manufacturing, evaluate Industry 4.0 applications to minimize labor and raw material requirements (e.g., additive manufacturing) as well as support cost curve reductions for potentially relocating sites closer to demand centers. Confirm internal alignment of your commercial strategy to understand the investment posture to prioritize and mitigate risks associated with your most strategic customers, product lines/offerings, and services.
- Enhance traceability by mapping your supply base from the top tier downwards, using tools that offer maximum visibility. Starting with a full mapping of the supply base, initiate a plan to achieve visibility at each tier of the value chain—from raw materials to finished goods to recycling—to improve operational, sustainability, regulatory, and resilience outcomes. Create a flexible long-term traceability roadmap to support the pragmatic sequencing of data, technology, and partnership investments required for successful test-and-learn pilots and enterprise scaling.
- Refine your operating model so your resilience strategy infuses the way your company is organized and governed, as well as the tools it uses. Deploy a cross-functional operating model that links business and operations functions to support proactive risk management and rapid recovery capabilities, utilizing the leading technology identified in the digital roadmap. Ultimately, strive to create a culture that views resilience as a necessary competitive advantage.
These actions can all improve supply chain resilience today and tomorrow. But the need to act far exceeds the usual obligations to stakeholders. As shown in the Covid-19 pandemic, when the consistent availability of groceries and other staples was a lifeline for many, keeping products and services flowing amid extreme turbulence can help to stabilize more than just businesses.