Operations Excellence
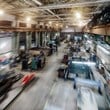
For nearly 20 years, Lean Six Sigma has defined excellence in operations. Companies that combined Lean manufacturing to eliminate waste with Six Sigma tools to improve quality deftly outmaneuvered the competition with lower costs and fewer defects. Now, as digital technologies proliferate, many companies are looking to increase their efficiency gains.
All too often, however, we see companies launch digital initiatives that are disconnected from Lean Six Sigma efforts. That’s a missed opportunity. Integrating digital technologies into a Lean Six Sigma system can turbocharge the benefits of both. Traditional Lean deployment delivers up to 15% in cost savings. In our experience, companies that use digital tools to enhance Lean Six Sigma efforts generate up to 30% or more in cost savings—and the payback time is faster (see Figure 1).
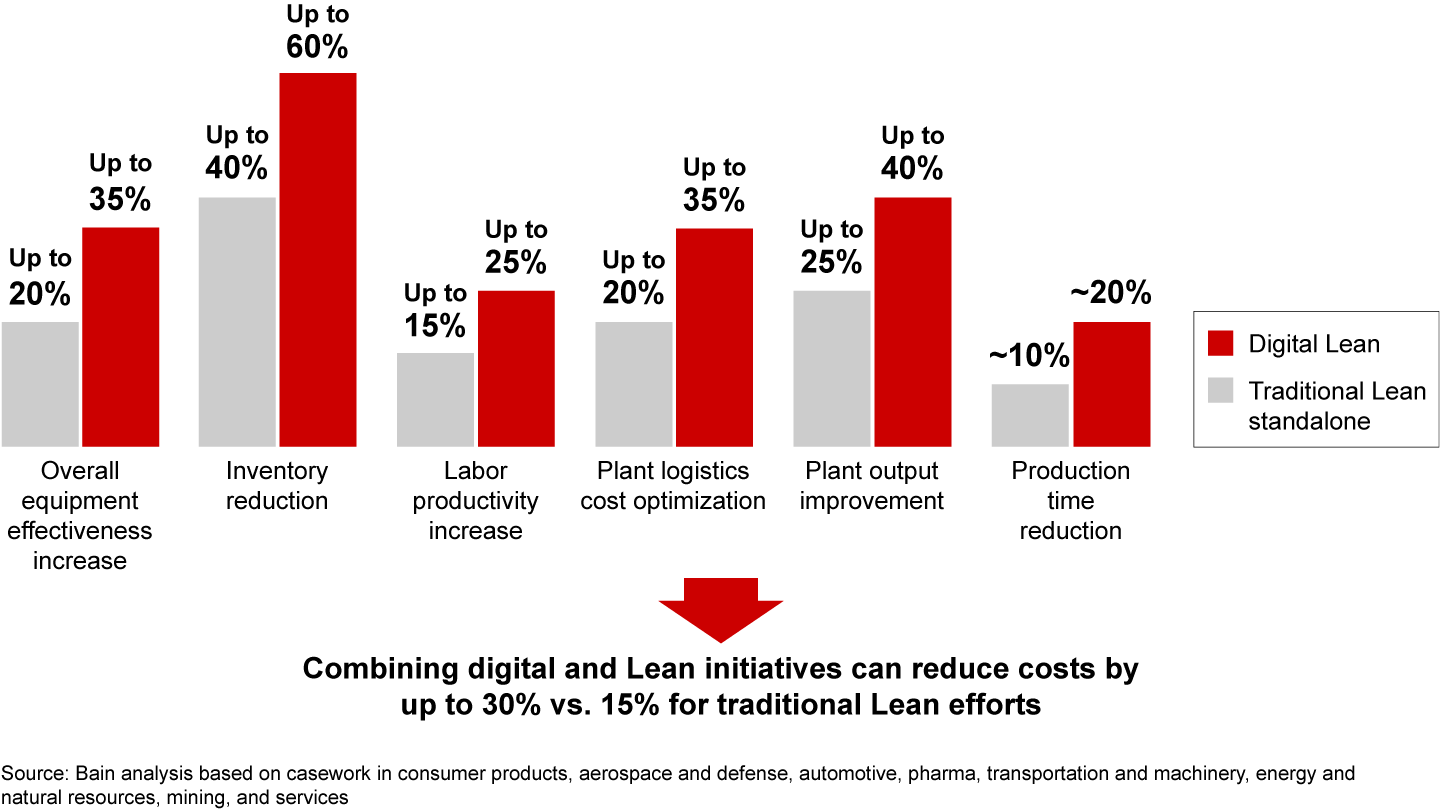

As data becomes more accessible, the number of digital tools aimed at the shop floor is growing rapidly. By 2020, the amount of data generated on an annual basis will be 40 times greater than it was in 2015, and the number of connected devices will double during that same period. Digital tools harness that data and connectivity to attack the same kind of waste that Lean manufacturing tackles—namely, transport, inventory, motion, waiting, overprocessing, overproduction and defects. They also improve worker safety.
Take the case of a large regional food processing company that was struggling with a growing number of near misses as the risk of accidents increased on its shop floor. The problem was the large number of forklifts and transport vehicles crisscrossing the shop floor. To mitigate the risks, the company slowed down the forklifts’ pace, which caused materials to fail to get to the production lines on time, defects to mount and efficiency to plummet.
To resolve the problem, the leadership team deployed autonomous guided forklifts and collaborative robots (cobots) together with remote light detection and ranging technology. Those moves improved the company’s production line margins by 19%, on average, thanks to lower costs and improved productivity. At the same time, the company standardized operators’ tasks and introduced cobots on risky, labor-intensive lines, reducing overall plant injuries by 50%.
Predictive analytics and machine learning are powerful digital tools that can enhance Six Sigma’s ability to reduce defects and produce better products more consistently. Traditionally, companies have relied on professional Six Sigma experts to run off-line simulation models to identify opportunities for process improvements and reduce defects. Leaders now use sensors to enable real-time sampling and real-time simulation software to optimize production schedules.
The same food processing company mentioned above improved its overall equipment effectiveness by 7 percentage points by using analytics software to optimize the production schedule. The biggest gains came from minimizing the equipment downtime required to adjust tooling when the company switches to a different product. When market demand shifted, the analytics software rapidly produced new, efficient production schedules.
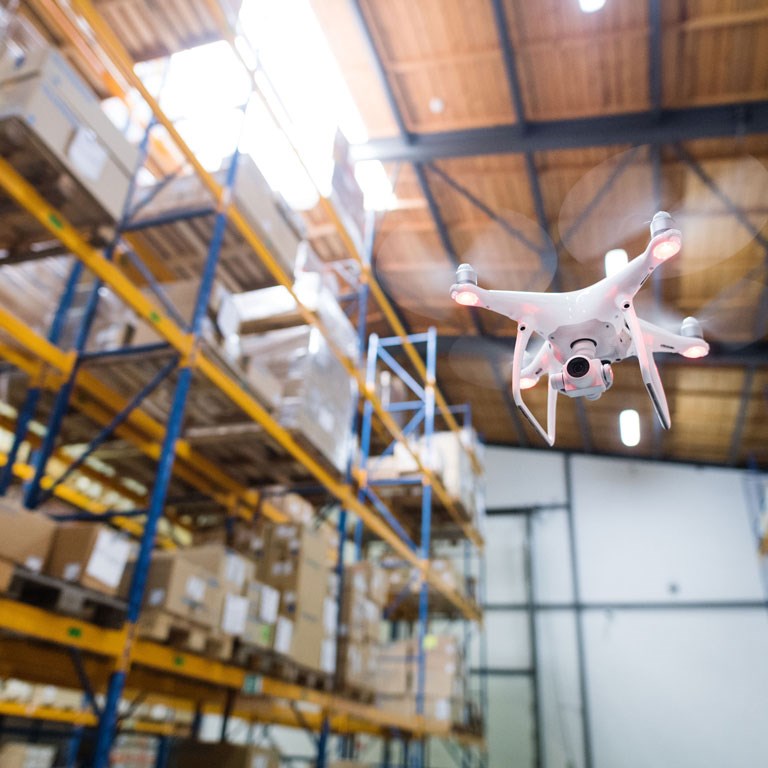
Operations Excellence
Companies with best-in-class operations have a strong competitive edge. Bain's insights on operational excellence help leadership teams transform supply chains, procurement strategy, and manufacturing capabilities into strategic weapons.
A raft of digital tools can help reduce waste on the shop floor, from remote and predictive maintenance technologies to smart logistics systems that improve sourcing and automated replenishment. One regional utility company deployed advanced analytics to help predict transformer failure, understand outage duration and identify opportunities to improve system reliability. The effort doubled (and sometimes tripled) the company’s ability to forecast failures and prevent outages, increasing customer satisfaction. It also reduced outage duration by 15% to 20%.
Digital technologies are creating a breakthrough opportunity for companies to increase efficiency and improve quality. But those that apply them in a vacuum are missing out on the biggest gains. Combining digital initiatives with Lean Six Sigma produces faster and better results than either initiative alone. Five years from now, it will be impossible to think Lean without thinking digital.
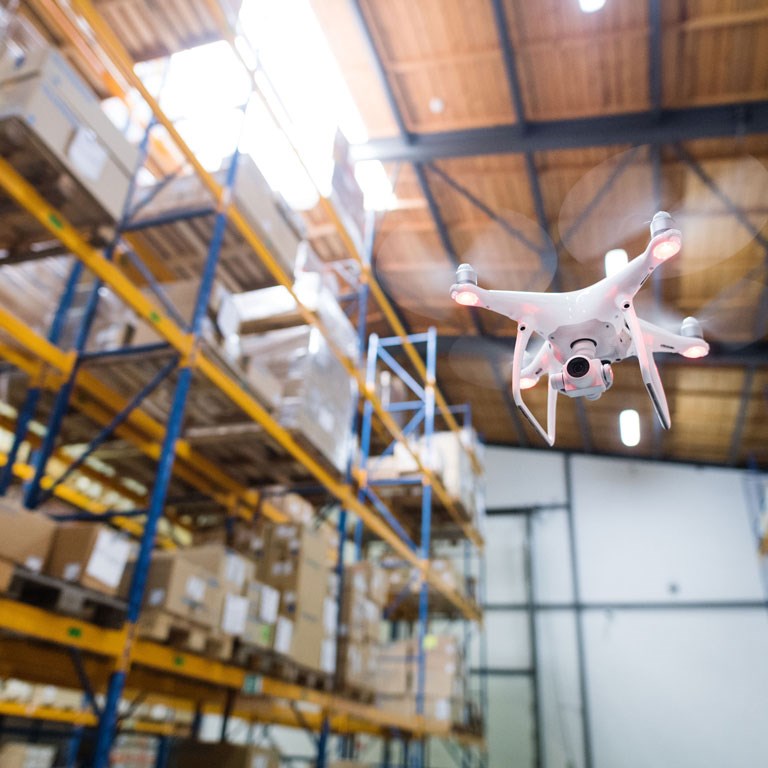
Operations Excellence
Companies with best-in-class operations have a strong competitive edge. Bain's insights on operational excellence help leadership teams transform supply chains, procurement strategy, and manufacturing capabilities into strategic weapons.
Pierluigi Serlenga is a partner with Bain & Company’s Performance Improvement and Advanced Manufacturing & Services practices; he is based in the firm’s Rome office. Marzio Forlini is a principal with Bain’s Performance Improvement practice; he is based in the firm’s Milan office.