Global Machinery & Equipment Report
At a Glance
- 70% of machinery customers expect more personalized or customized products than they received three years ago.
- In a closed-loop engineering system, every phase of a product’s life cycle feeds back data into the system.
- Leading companies implementing closed-loop product life cycle management have reduced time to market by more than 20%.
This article is part of Bain's Global Machinery & Equipment Report 2024
Faster, cheaper, and customized. These three key words are on the mind of every machinery executive striving for innovation. Closed-loop product life cycle management (PLM) can help achieve all three by cutting time to market, reducing costs, improving quality, and enabling product customization.
Closed-loop PLM includes the set of processes and technologies that manage the entire life cycle of a product, from conception to end of life. In a closed-loop system (also referred to as a digital thread or closed-loop engineering), data is collected in real time from every life cycle phase, which enables ongoing optimization.
It’s not easy to implement, but the benefits of closed-loop PLM are significant. Leading companies using closed-loop PLM have improved their on-time delivery by more than 20% and reduced time to market by more than 20%, according to Bain research. They have also been able to reduce R&D costs by 10% to 15% (see Figure 1).
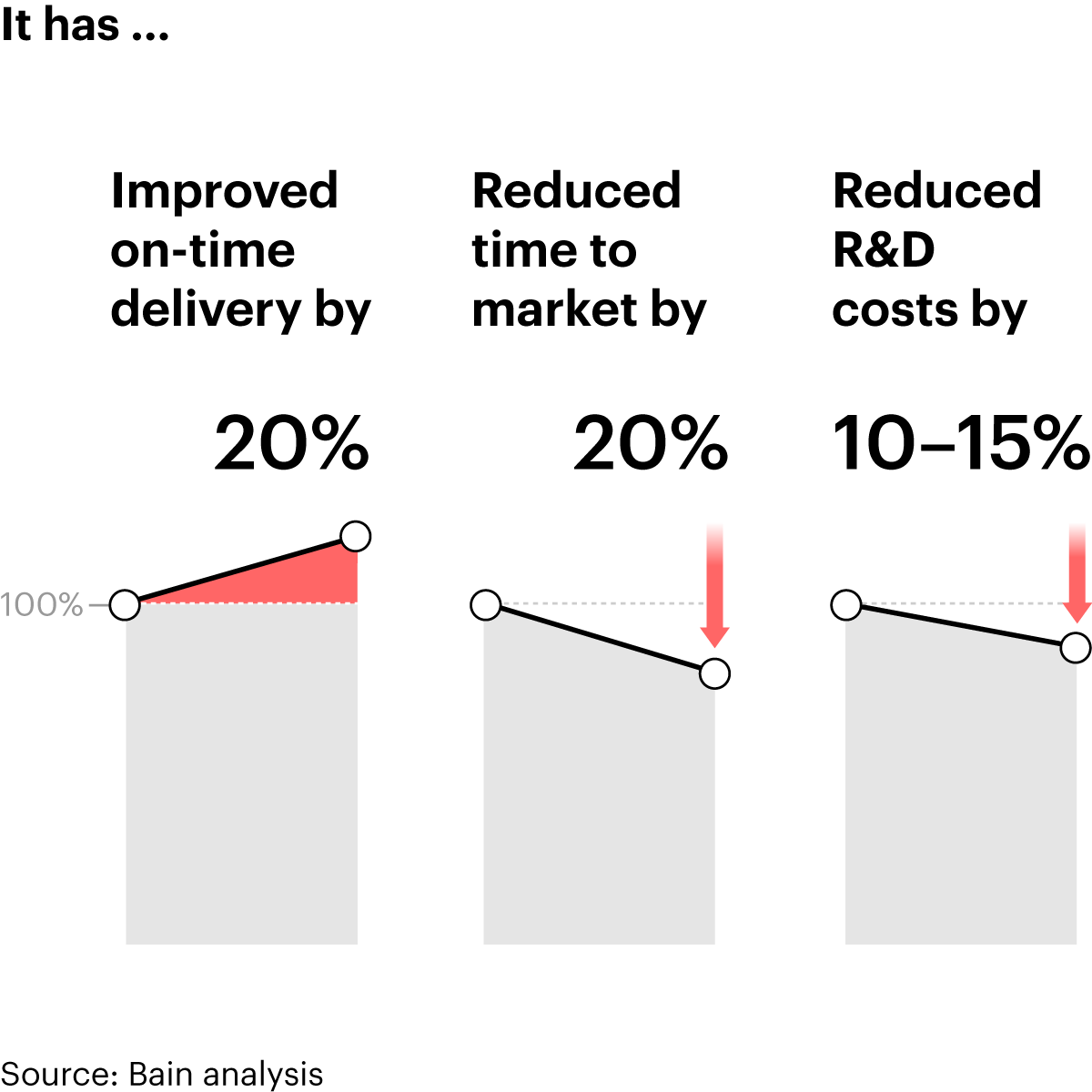
High expectations from customers
Producing products faster and with a greater degree of customization has become table stakes for machinery and equipment companies. In fact, 68% of customers expect the same quality of products they received three years ago, but more quickly. And 70% of machinery customers expect more personalized or customized products than they received three years ago, according to Oxford Economics.
Delivering products that meet these expectations, however, poses a challenge given the complexity linked to customization. Streamlining design, iteration, and validation stages can also be difficult when dealing with complex PLM, computer-aided design, and computer-aided manufacturing systems; multiple iterations; and collaboration among engineering teams.
Faster
Many machinery leaders have gotten the memo from customers: Among the top priorities in engineering and R&D for machinery companies over the next three years is shortening time to market, according to Bain research.
Integrating hardware and software rapidly with zero defects has always been difficult. It’s even harder now with a widening base of code and hardware. And that’s not to mention the challenges of combining two different development approaches: Software development requires ongoing iteration in contrast to hardware development, which is generally very sequential.
Closed-loop PLM can help address these challenges. This approach includes IT tools, such as PLM software, as well as operations, management, governance, and organizational structure. In short, it’s not just about reducing the number of engineering changes; all functions and businesses are brought into closed-loop PLM (see Figure 2).
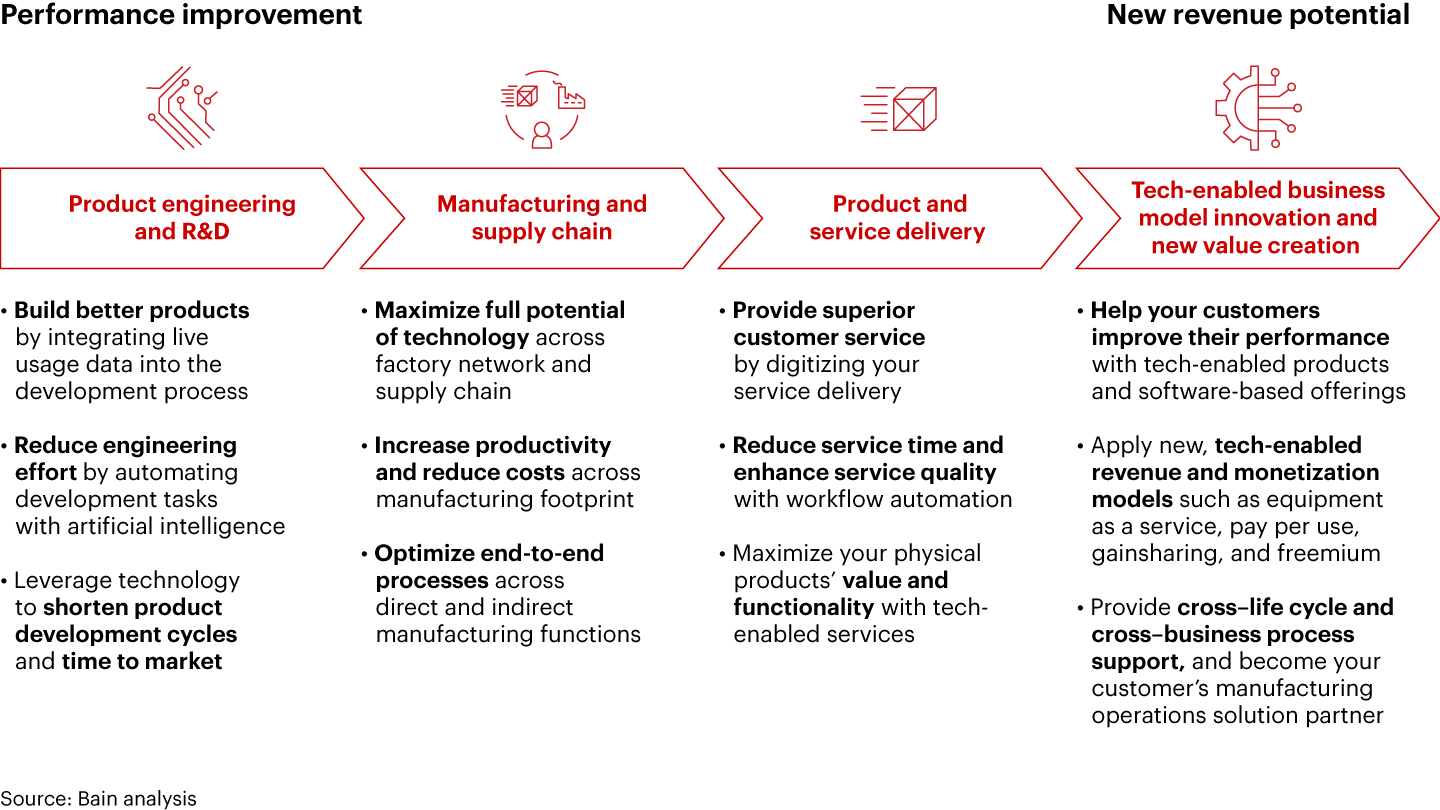
Our research shows that closed-loop PLM reduces time to market by more than 20% by enhancing parallel process development. Specifically, it allows cross-functional teams that could be working in different locations to develop products together using digital tools and in parallel with other teams. These teams can make data-driven decisions more quickly. The collected data also provides more transparency in the supply chain so that there is a single source of truth in terms of the cost of components, for instance. Finally, defect feedback from earlier models can automatically and simultaneously be fed back into new product development.
Emerging leaders are finding other benefits, too. Olbrich, a developer of customized machine solutions and factory design, deployed a PLM system that has reduced the time to prepare a quotation by more than 50%. Olbrich can also now design factory plants more quickly as it can reuse certain design aspects. It is also able to create new projects faster and more easily since article, customer, and project data are automatically added from the quotation phase. Finally, the company has greater transparency into ongoing projects thanks to real-time evaluation of projects’ progress.
Cheaper
Beyond the obvious cost savings from speeding up time to market, a closed-loop PLM approach enables better access to product data and an increased ability to reuse designs in product development. It also facilitates better management of the bill of materials. Since all components are logged, estimations of product costs are more accurate. Companies that use closed-loop PLM have lower R&D costs as the collaborative approach requires fewer engineers to develop a product.
The cost reductions can be significant. Kampf, a manufacturer of slitting and winding machines, has built a powerful product data management system that reduced error costs by 50% and increased productivity by 15% to 20%.
Higher quality
A closed-loop PLM approach provides a much more structured way to integrate data from various sources to better understand customer needs, analyze customer insights, and manage customer requirements. Companies that make the most of this data during product development have an edge when tailoring and customizing their products. In addition to helping companies listen to their customers, a closed-loop PLM approach allows them to gather learning about usage patterns from products in the field.
In closed-loop systems, it is possible to solicit and collect feedback from customers and the market during the life cycle of the product and feed it directly into the development of next-generation products. The closed-loop PLM approach also enables more comprehensive quality management and asset management systems as it integrates data flow between the two (see Figure 3).
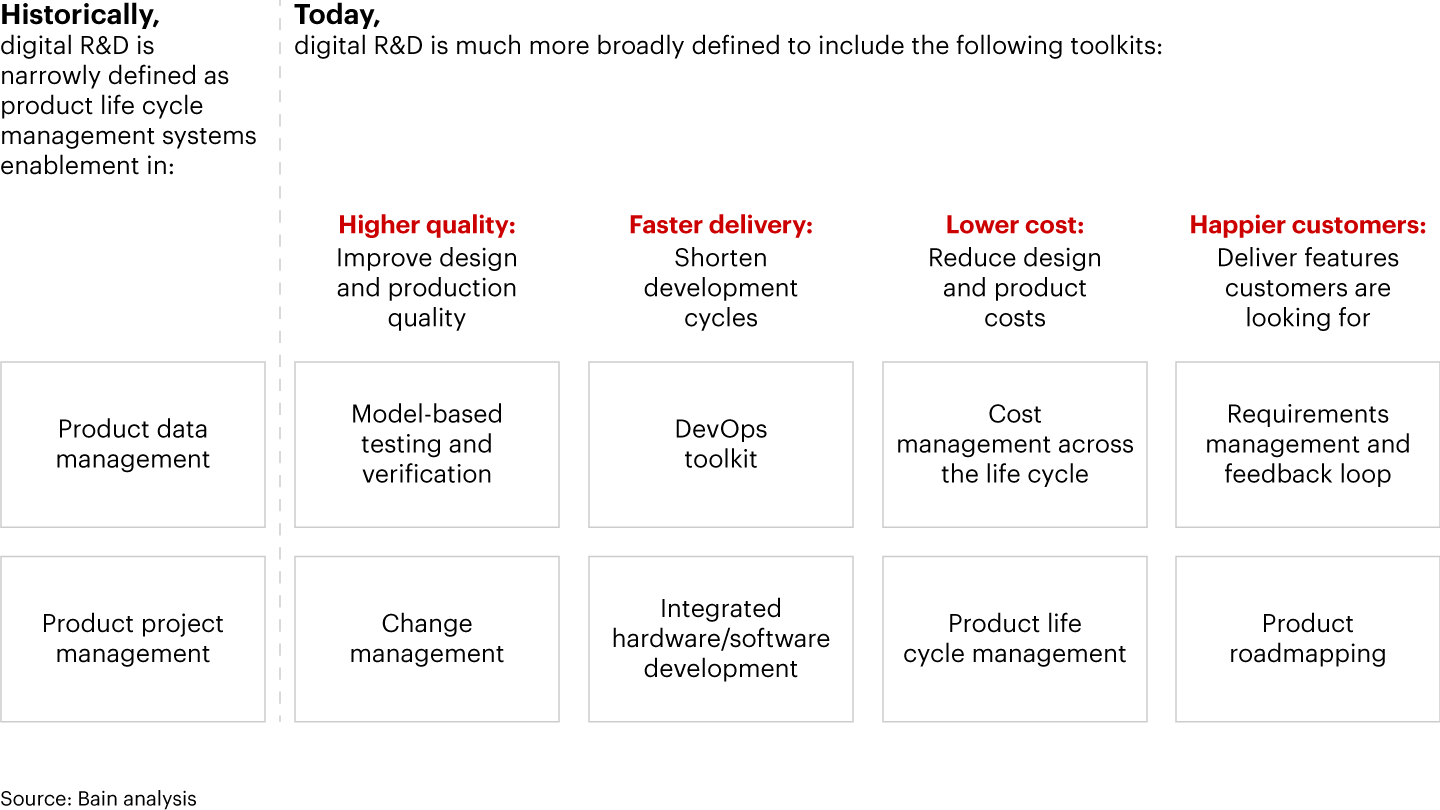
Where to begin with closed-loop PLM
Strategy: Ask which business objectives you are trying to meet with a closed-loop PLM approach. These may include reducing R&D costs, speeding time to market, gaining market share, getting closer to customers, or becoming an innovator with best-in-class technologies.
Organization: Adopt a mindset to act cross-functionally within your organization. Communicate to employees the integral role of closed-loop PLM. Upskill existing employees, and hire new talent with expertise in closed-loop PLM.
Data: Analyze how product data is currently used in product development. Identify high-priority use cases that allow quick deployment of digital twins and scalability in product development. Also, ensure an online connection of equipment or machinery so that any type of usage patterns or data about defects can flow directly back to product development.
Technology: Determine which technology system supports any missing elements and improves related key performance indicator gaps. Be 100% transparent, and communicate clearly to machinery users which types of data are collected and go into tools such as the digital twin. Many technology companies, such as phone companies, have end user agreements that define how usage data is being shared and used for future product development.
Closed-loop PLM is a huge investment, but it also presents a tremendous opportunity. Companies that start now and work with partners that can share lessons learned from those already reaping the benefits of closed-loop PLM have the chance to leapfrog ahead of competitors in the coming years.